Link zur deutschen Version: Tragverhalten eines CFK-vorgespannten Bahnbrückenprototyps
After my last blog post on the production of Switzerland’s first CFRP prestressed railway bridge prototype, the “prototype” project was essentially over for me, and I was looking forward to doing some serious science from my office chair again – preferably something including AI. Over the course of the summer, however, the question of what to do with this somewhat clunky thing crept back up on us: Especially given its superior durability properties, it couldn’t stand around in our lab forever. Put it up in the coffee room as a vertical flower box? Launch it into space to market our flagship sustainability project? With a weight of 10 t, the prototype would only be marginally heavier than the red Tesla that has been doing its rounds there for years… After both ideas had to be scuttled primarily due to excessive internal ETH bureaucracy (ever tried to get a permit from a federal office for launching a rocket?), the idea of testing the prototype for its load-bearing behaviour came up. Pretty wild, someone would have had to build a test rig with a capacity of 3 MN and have installed optical fibres for strain measurements on the reinforcement and prestressing already during the production of the prototype…
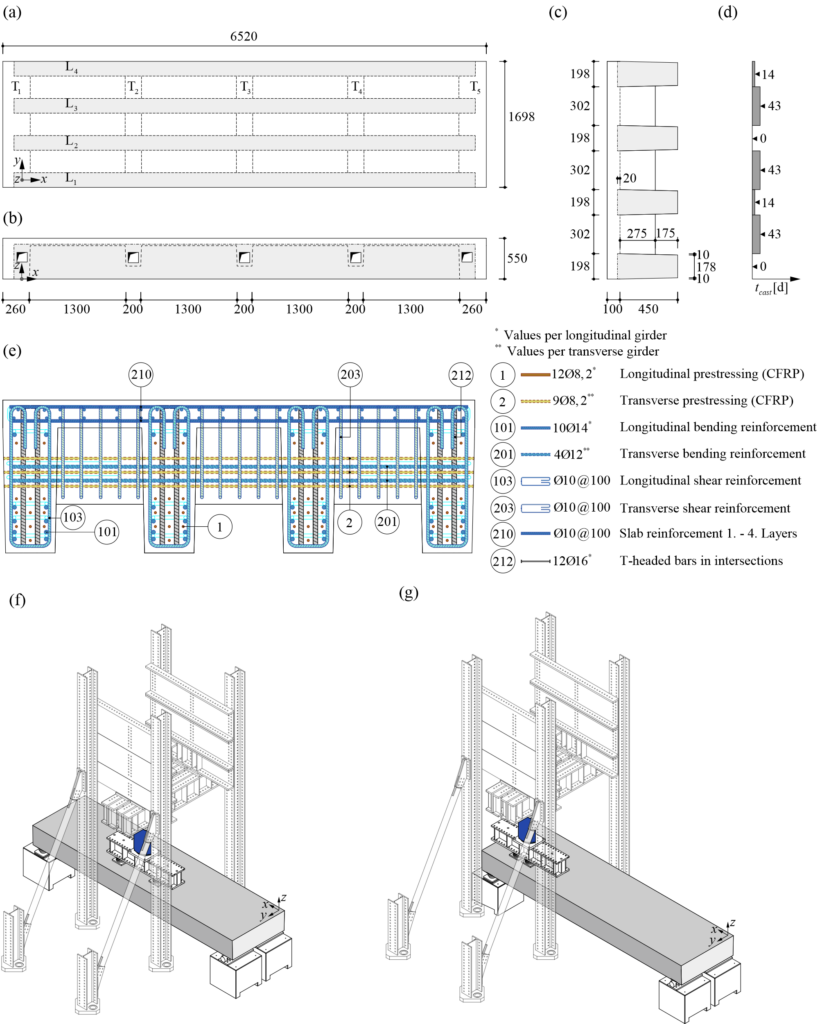
In addition to demonstrating the feasibility of the production, the aim of testing the prototype was a “proof of concept” regarding the load-bearing behaviour of the material “CFRP-prestressed steel-reinforced concrete” and its suitability for railway bridges. The following questions were therefore of central importance:
- Does the anchorage of the pretensioned CFRP rods work as anticipated via bond with the concrete? In particular, does it also function under cyclic loading and loads positioned in the vicinity of the supports?
- How does the composite material behave in the ultimate limit state? Do we achieve the desired bending failure mechanism “concrete failure at yielding of the reinforcing steel” and a certain plastic deformation in the reinforcement despite the brittle CFRP?
- How does the prototype behave under loads close to the support, which type of shear failure occurs? What compression field inclinations can be assumed in the shear verification of high-performance concrete with CFRP-prestressing?
Short disclaimer: I cannot go into these questions in detail in this blog post. For detailed test analyses and interpretations, interested readers are referred to our scientific publications (e.g. here). But first things first: Figure 1 provides an overview of the prototype and the test setup of the bending and shear test. The prototype consisted of four CFRP-prestressed longitudinal and three transverse girders (in the span) and was initially subjected to four-point bending. The loads were applied to the second of four longitudinal beams, thus eccentrical in the cross-section. After 60’000 load cycles at three different load levels, the specimen was tested to failure, whereby the failure mechanism was concrete crushing at yielding of the reinforcing steel with subsequent (clearly audible) rupture of the first CFRP rods at mid-span. The test rig was then slightly modified and a shear test was carried out in an intact area of the specimen, which was rotated by 180° before reinstalling.
Videos 1 (time-lapse recording) and 2 (end of test) show excerpts from the bending test. It is important to emphasise that despite the concrete crushing in the bending compression zone (see Video 2), which extended over almost the entire width of the specimen, and despite the rupture of individual CFRP rods (Video 2 with sound), no total collapse of the prototype took place.
In combination with Figure 2 (load-deformation in bending and shear tests, image of shear failure), the videos provide insight into some, but not all, of the questions formulated in the beginning:
- The prestressing remained intact during the entire test series, which is demonstrated by the “re-erection” of the specimen after the bending test (see Video 1). Unfortunately, it was not possible to conclusively determine the extent to which the anchorage zones of the CFRP rods had extended due to the cyclic loading and the shear load, as the optical fibres on the pretensioned CFRP rods of the longitudinal beams did not work during the tests.
- The intended bending failure mechanism was achieved. In three out of four longitudinal girders, the reinforcing steel was yielding at the end of the bending test, which resulted in a redistribution of forces in the specimen. Figure 2 (a) shows (i) how all four longitudinal girders were activated and (ii) the significant deformation capacity after reaching the maximum load (failure of the concrete compression zone). At this maximum load, there was no significant force drop in the deformation-controlled test setup. Instead, the system was able to deform considerably under approximately constant load before the test was stopped.
- All four longitudinal girders were also activated under loading close to the support, as can be seen in the load-deformation diagram of the shear test in Figure 2 (b). As expected, the shear failure occurred in the loaded girder L2, with a shear force in the longitudinal girder of approx. 900 kN. This leads to the conclusion that the stirrups were yielding, but the failure occurred in the concrete, as shown in Figure 2 (c), at a fairly steep compression field inclination of about 35-40°. Consequently, there were no “rotating cracks” with flat inclinations at the end (compare to admissible compression field inclinations in prestressed structures according to SIA 262), which is not unusual for high-performance concrete due to its low crack roughness.
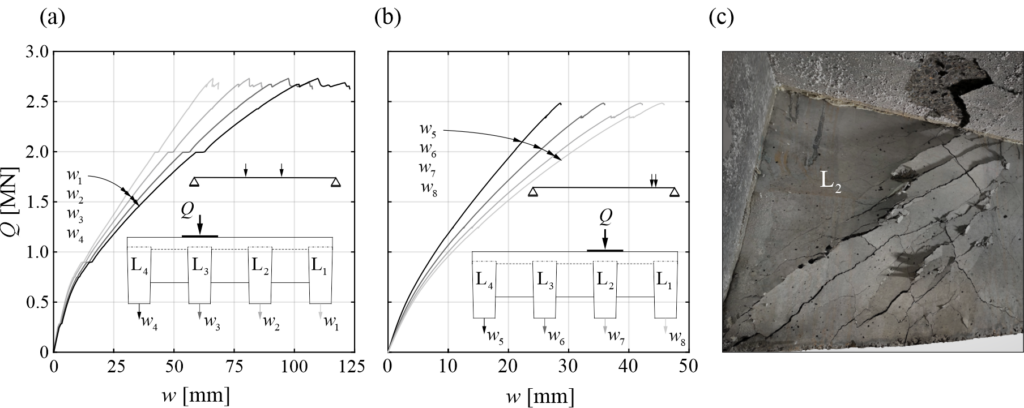
From the project team’s point of view, the proof of concept was successful. The system behaves as anticipated in bending, and the reinforcing steel brings a certain plastic deformation capacity into the system. The prestressing is robust but needs to be investigated in further detail. The same applies to the shear behaviour. What does that mean? As part of the current project phase “Scientific work” (phase 3 of 5 on the way to the actual construction of a CFRP-prestressed railway bridge on the SBB network), further tests are pending; the static and cyclic shear tests on individual CFRP-prestressed T-beams will be particularly interesting. In parallel to the test campaign, we are now developing mechanical models and verification concepts. It also means that the AI-thing will have to wait… stay tuned!
Andreas Näsbom
Literatur
[1] | A. Näsbom, K. Thoma and W. Kaufmann, “Construction and testing of a CFRP-prestressed railway bridge prototype”, in IABSE Symposium Manchester 2024, Manchester, Apr. 2024. |