Link to the English version: Production of a CFRP-Prestressed Railway Bridge Prototype.
Seit dem letzten Blogpost zum Thema ist einige Zeit vergangen, in der sich entsprechend viel getan hat. Dem Ziel, Bahnbrücken im Spannweitenbereich von 2-10 m mit karbonfaserverstärktem Kunststoff (CFK) vorzuspannen, ist das Projektteam bestehend aus SBB, alphabeton AG, HSLU, Empa und ETH einiges nähergekommen: Es ist gelungen, einen 1.7 m x 6.5 m grossen Prototypen zu bauen. Der Prototyp ist biaxial CFK-vorgespannt und repräsentiert einen Ausschnitt (bestehend aus vier anstelle von neun Längsträgern) einer Überführung mit 6 m Spannweite. Die Vorspannung ist dabei so ausgelegt, dass die Brücke unter Gebrauchslasten (LM1) ungerissen bleiben soll. Abbildung 1 zeigt die Grundidee des Brückensystems sowie den nichtrostenden Bewehrungsstahl und die sandbeschichteten CFK-Spannstäbe.
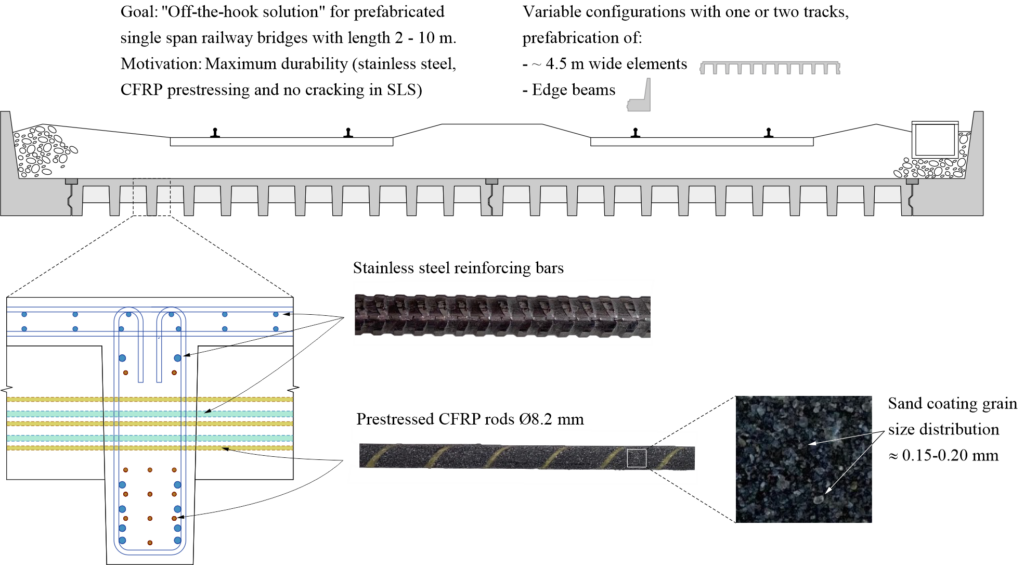
Der detaillierte Bewehrungsplan des Prototyps im Querschnitt ist in Abbildung 2 gezeigt. Er beinhaltet folgende Elemente:
- CFK-Spannstäbe (Längsvorspannung Pos. (1), Quervorspannung Pos. (2))
- Biegebewehrung der Längs- (101) und Querträger (201) aus Duplex Stahl mit Werkstoffnummer 1.4362
- Bügel und Plattenbewehrung (im Prototyp aus Kostengründen in herkömmlichem B500B Stahl)
- Aufhängebewehrung in den Kreuzungsbereichen der Längs- und Querträger (Pos. 212)
- Transportanker in den äussersten Längsträgern
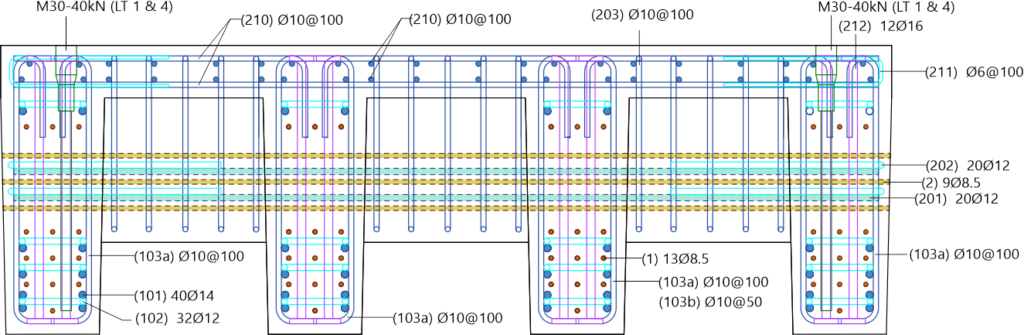
Zwei wesentliche Änderungen im Konzept und dem Herstellungsverfahren wurden seit dem letzten Blogbeitrag vorgenommen:
- Anstelle eines Ultrahochleistungsbetons (UHB) wurde ein Hochleistungsbeton C80/95 verwendet. Vorversuche haben gezeigt, dass dieser Beton ausreichend ist, um die im Spannbettverfahren vorgespannten CFK-Stäbe über Verbund zu verankern – bei wesentlich kleinerem Zementgehalt als der UHB.
- Die Herstellung erfolgte schrittweise: In einem ersten Schritt wurden die Längsträger (jeweils zwei hintereinander mit den gleichen Spannstäben vorgespannt) betoniert. Nach Fertigung der vier Längsträger wurden diese nebeneinander platziert, um die vorgespannten Querträger (Quervorspannung und -bewehrung durch Aussparungen in den Längsträgern) und die Platte zu betonieren.
Für die Herstellung (Vorspannung im Spannbettverfahren) des Prototyps waren umfangreiche Technologieentwicklung und Vorarbeiten vonnöten. Dies betrifft einerseits die Entwicklung von insgesamt vier Spannrahmen für die Vorspannung in Längs- und Querrichtung, federführend projektiert durch Prof. Dr. Albin Kenel und Martina Rohrer, HSLU. Renderings der Spannrahmen sind in Abbildung 3 zu sehen. Der Spannrahmen für die Längsträger (Abbildung 3 (a)) ist insgesamt gut 14 m lang (wobei er modular auf beliebige Längen <14 m einstellbar ist) und auf eine totale Spannkraft von 2.8 MN ausgelegt. Die drei Rahmen für die Quervorspannung (Abbildung 3(b)) müssen wesentlich weniger Last (~0.8 MN) verankern können. Das Grundsystem ist überall identisch: die CFK-Stäbe werden in Lochplatten verankert, die über hydraulische Pressen verschoben werden können, um die gewünschte Spannkraft auf die Stäbe zu bringen. Anschliessend wird um die gespannten Stäbe betoniert; die Vorspannung wird abgesenkt sobald der Beton die nötige Festigkeit aufweist.
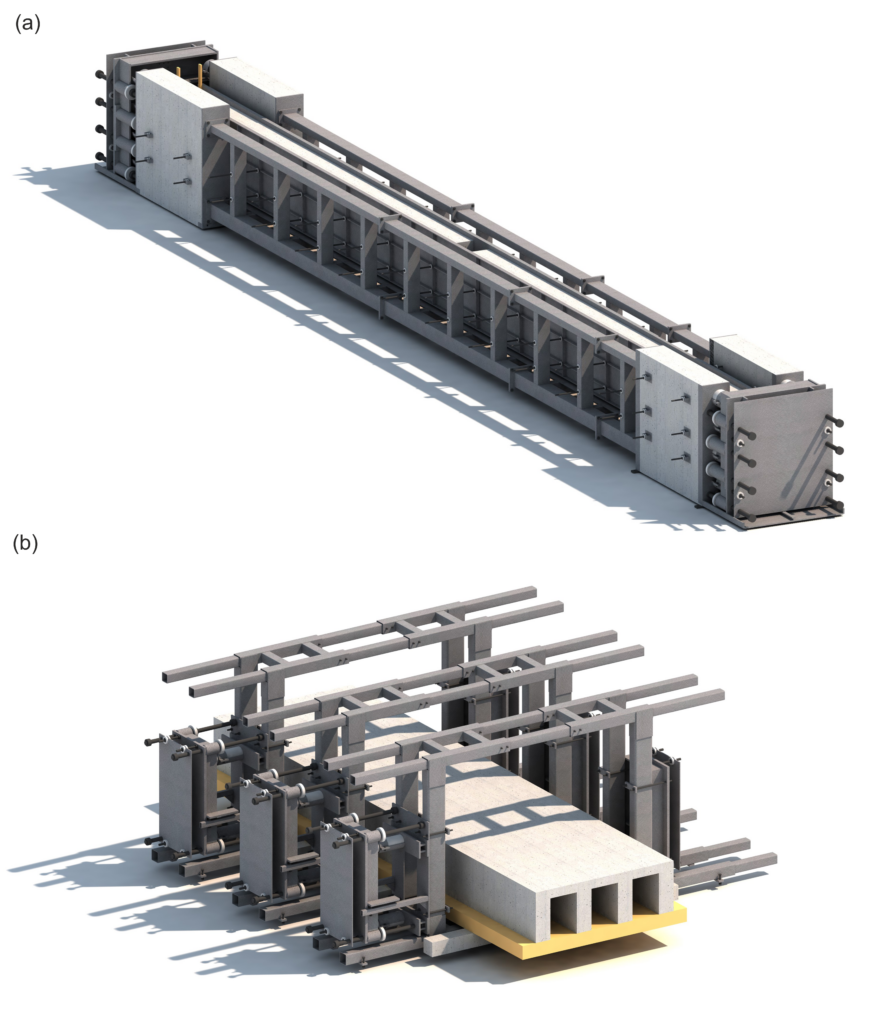
Die zweite grosse Herausforderung war die Keilverankerung der aufgrund ihrer Anisotropie äusserst anspruchsvoll zu spannenden CFK-Stäbe. Die Verankerung (entwickelt durch Prof. Dr. Giovanni Terrasi und Valentin Ott, Empa) bestehend aus einer Stahlhülse und drei Kunststoffkeilen ist auf ihrem jetzigen Entwicklungsstand in der Lage, zuverlässig eine Kraft von 55 kN pro Stab (entspricht einer Spannung von 1041 MPa bezogen auf den nominellen Durchmesser von 8.2 mm) zu verankern. Abbildung 4 zeigt (a) eine einzelne Verankerung, (b) das hydraulische Einpressen der Keile auf eine definierte Einpresskraft, sowie (c) die Anordnung der Keile in der Lochplatte für die Herstellung der Längsträger.
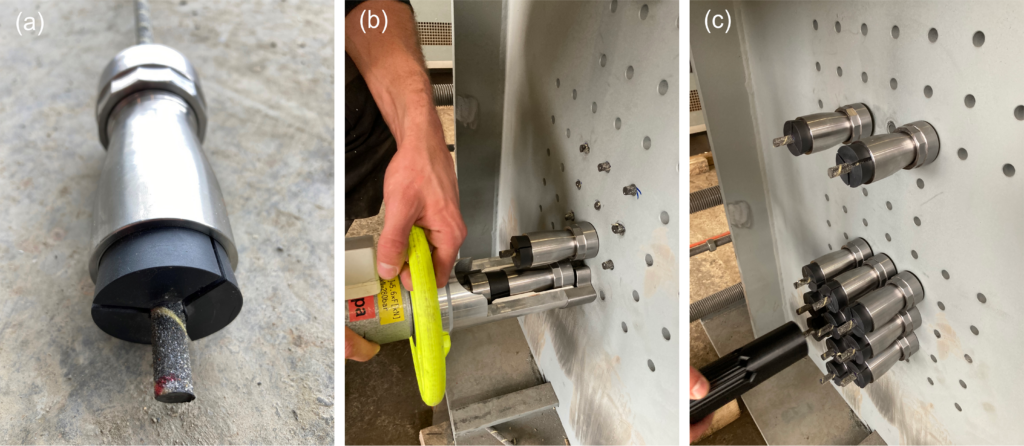
Abbildung 5 zeigt Bilder der Herstellung im Werk der alphabeton AG:
(a) | Bewehrungskörbe der Längsträger im Spannrahmen. Diese mussten äusserst präzise gefertigt sein, damit die Spannglieder durchgeführt werden konnten ohne die Bewehrungseisen zu touchieren (vgl. Abbildung 2). Kontakt würde (i) zu nicht kontrollierbaren Umlenkungskräften und schlimmstenfalls Versagen der Spannstäbe führen, und (ii) das Risiko galvanischer Korrosion der Bewehrungsstäbe erhöhen. |
(b) | Bewehrungskörbe mit den unteren Lagen der CFK-Spannstäbe inklusive der horizontal geteilten Abschalung. |
(c) | Bewehrungskorb inklusive CFK-Spannstäbe. |
(d) | (a) Detail der Aussparungen inklusive Aufhängebewehrung (im Kreuzungsbereich der Längs- und Querträger) und eigens für diesen Zweck an der Empa 3D-gedruckte Abstandhalter, die auf das Längseisen montiert werden konnten. So konnte die geforderte Präzision der Aussparungen für das Durchführen der Quervorspannung sichergestellt werden. |
(e) | Längsträger in der Schalung nach dem Betonieren. |
(f) | Platzierung der Längsträger in den Spannrahmen für die Quervorspannung. |
(g) | Bewehrung der Endscheiben und Brückenplatte. |
(h) | Einpressen der Keile für die Quervorspannung. Man beachte, dass während des Spannvorgangs massive Stahlplatten hinter die Verankerungen montiert wurden, um ein allfälliges unkontrolliertes Absprengen bei potentiellem Versagen der Spannstäbe zu verhindern (siehe Abbildung 3). |
(i) | Detail der Quervorspannung in den Aussparungen der Längsträger. |
(j) | Fertiger Prototyp: Seitenansicht. |
(k) | Fertiger Prototyp: Ansicht von unten mit Längs- und Querträgern. |
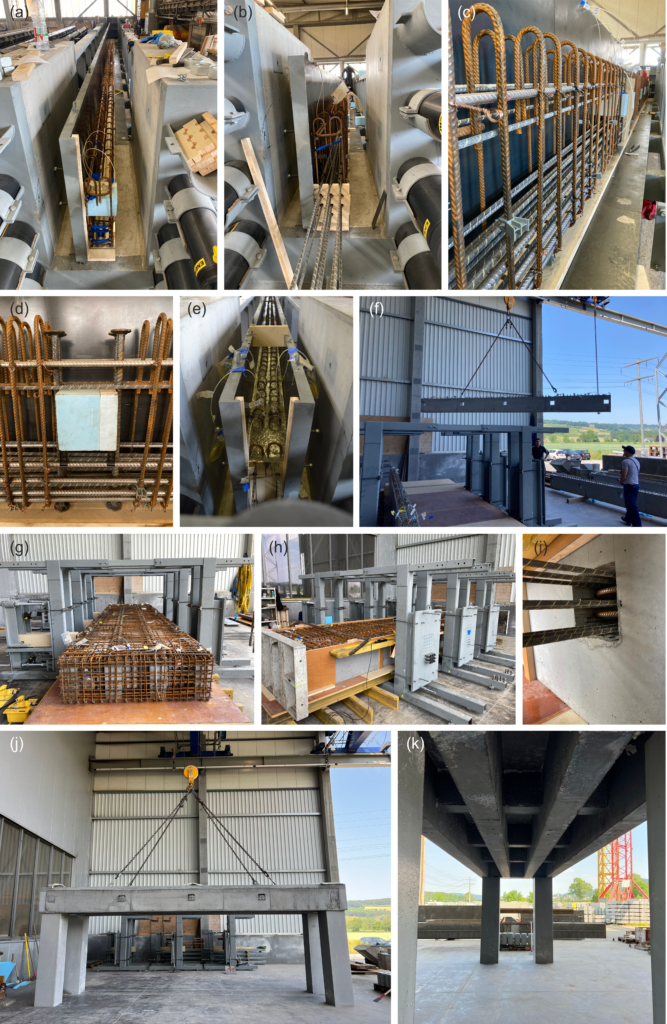
Als Fazit lässt sich festhalten, dass die Herstellung des Prototyps wie geplant gelungen ist. Erste faseroptische Dehnungsmessungen an den CFK-Stäben zeigen, dass die Vorspannung auf einer Länge von weniger als 200 mm voll über Verbund verankert wird und die Spannbettvorspannung mit sandbeschichteten CFK-Stäben somit funktioniert. «Lessons learned» umfassen sowohl das Design als auch die Ausführung. Statische Effizienz muss sorgfältig gegen die Komplexität der Fertigung abgewogen werden; der eine oder andere Millimeter mehr zwischen CFK – und Bewehrungsstäben hätte die Herstellung des Prototyps erheblich vereinfacht. Das Vorspannen der CFK-Stäbe ist anspruchsvoll und bedarf neben massgeschneiderter Hardware wie Spannrahmen und Keilankern äusserst präziser Arbeit im Werk, insbesondere beim Binden der Bewehrungskörbe. Aus Sicht des Projektteams hat die alphabeton AG den «Proof of concept» für die Herstellung erbracht, der Weg zum Bau der ersten Bahnbrücke aus CFK-vorgespanntem Beton ist jedoch noch weit… Stay tuned!
Andreas Näsbom