Link to the English version: The path to more sustainable concrete floor slabs through digital fabrication
In Anbetracht der Klimakrise müssen die Treibhausgasemissionen drastisch reduziert werden. Dabei muss auch der Gebäudesektor, welchem rund 37 Prozent der globalen betrieblichen energie- und prozessbedingten Treibhausgasemissionen zugeordnet werden, deutlich umweltfreundlicher werden, insbesondere wenn man bedenkt, dass die benötigte Fläche für Wohnen und Infrastruktur in den kommenden Jahren massiv zunehmen wird (2022 Global Status Report for Buildings and Construction). Um diese Reduktion der negativen Umweltauswirkungen zu erreichen ist ein Umdenken auf allen Ebenen nötig. Während aktuell alternative Baustoffe in der Forschung und Praxis grosse Beachtung finden, ist die Umsetzung von effizienten Tragwerken eine oft unterschätzte Massnahme, mit welcher enorme Einsparungen erreicht werden können. (The Institution of Structural Engineers, 2022)
Da in typischen Gebäuden rund die Hälfte des Materials in Decken verbaut wird (Bischof et al. 2022), liegt es nahe, Optimierungen der Materialeffizienz in diesen Bauteilen anzustreben. Tatsächlich existieren zahlreiche praxiserprobte Deckensysteme, welche im Vergleich zu den weitverbreiteten Flachdecken massiv reduzierte Treibhausgasemissionen verursachen: Durch die Wahl von statisch effizienten Systemen wie beispielsweise Rippendecken, Kassettendecken oder Hohlkörperdecken können in Abhängigkeit der Spannweite bis zu 60% der Treibhausgasemissionen im Vergleich zu Flachdecken eingespart werden (Regúlez et al., 2022). Wieso also bauen wir auch heute noch überwiegend Flachdecken?
Dies lässt sich mit einer ganzheitlichen Betrachtung des Problems erklären: Deckensysteme werden nicht oder nur bedingt aufgrund ihrer Treibhausgasemissionen gewählt. Vielmehr sind Kriterien wie Baukosten, Bauzeit, Schallschutz, Möglichkeit zur Integration von Haustechnikeinlagen und viele weitere entscheidend. Anders ausgedrückt müssen Deckensysteme sowohl ökologisch nachhaltig (u.a. Emissionen, Ressourcenverbrauch und Abfallproduktion, Dauerhaftigkeit und gegebenenfalls Zirkularität) als auch sozial nachhaltig (u.a. Sicherheit, Funktionalität und Anpassungsfähigkeit) und wirtschaftlich nachhaltig (u.a. Kosten, Baubarkeit und Flexibilität) sein, um auf dem Massenmarkt Verbreitung zu finden und so wirkungsvoll zur Steigerung der Umweltfreundlichkeit beizutragen. Die Komplexität dieser Anforderungen ist in Abbildung 1 zusammengefasst.
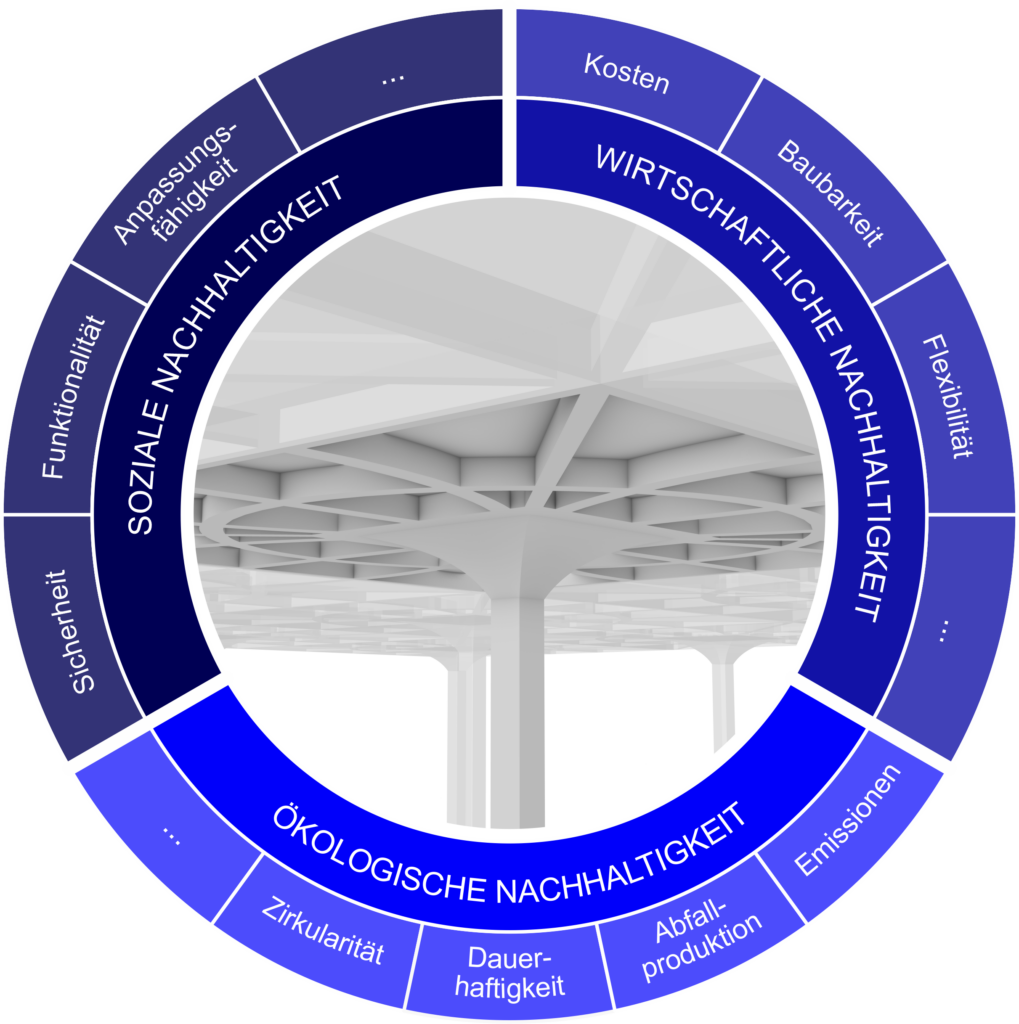
Bei vielen dieser Kriterien ist die Wahl einer Flachdecke, deren Produktion jahrzehntelang optimiert wurde, vorteilhaft: Nicht nur sind Flachdecken günstig in der Erstellung, sondern sie weisen auch eine niedrige Gesamthöhe und gute akustische Schalldämmeigenschaften auf und bieten die Möglichkeit, Haustechnik als Deckeneinlagen zu integrieren. Auch nicht zu unterschätzen ist die geometrische Freiheit im Grundriss, welche durch die Wahl von Flachdecken ermöglicht wird: Die statische Effizienz, welche mit Tragsystemen wie zum Beispiel Rippendecken erreicht wird, bedingt häufig eine höhere geometrische Komplexität der Querschnitte. Wegen des dafür erforderlichen höheren Schalungsaufwandes werden solche Decken im Allgemeinen nicht im Ortbetonverfahren sondern mittels Vorfabrikation hergestellt, wobei wiederverwendbare Schalungen eingesetzt werden. Dies wiederum reduziert die geometrische Freiheit der damit herstellbaren Grundrisse, da sich solch wiederverwendbare Schalungen im Allgemeinen nur für regelmässige und sich wiederholende Grundrisse eignen. Auch tragen Deckensysteme wie Rippendecken und Hohlkörperdecken primär in eine Richtung (in Gegensatz zu Flachdecken), was die geometrische Freiheit im Grundriss weiter eingrenzt.
All diese Gründe führen dazu, dass in der Praxis trotz des in den letzten Jahren gesteigerten Nachhaltigkeitsbewusstseins die Wahl häufig auf eine emissionsintensive Flachdecke fällt.
Das innovative Feld der digitalen Fertigung mit Beton (DFB) könnte dazu beitragen, dass diese Wahl in Zukunft häufiger auf ein effizienteres Tragsytem fällt: Durch eine Vielzahl von Fertigungsverfahren, das Bekannteste davon der 3D-Druck mit Beton (3DDB), soll der Bau von geometrisch komplexen, massgefertigten Bauteilen ohne oder nur mit minimaler Schalung bei reduzierten Produktionskosten und gesteigerter Arbeitssicherheit ermöglicht werden (Wangler et al., 2016). Was diese geometrische Freiheit in der Praxis bedeuten könnte, ist in Abbildung 2 ersichtlich: Für einen Grundriss wurden eine konventionelle Flachdecke, eine Rippendecke mit geraden, regelmässigen Rippen und eine Freiform-Rippendecke, wie sie potentiell mithilfe von digitalen Fertigungsmethoden produziert werden könnte, vordimensioniert. Aufgrund des direkteren Lastabtrags sind nicht nur die potentiellen Materialeinsparungen bei der Freiform-Rippendecke grösser als bei der Rippendecke mit geraden Rippen (27% – 38% anstatt 18% – 28% weniger Betonverbrauch in der Decke), sondern es resultieren weniger Anpassungen im Grundriss (wie zum Beispiel zusätzlich benötigte Stützen).
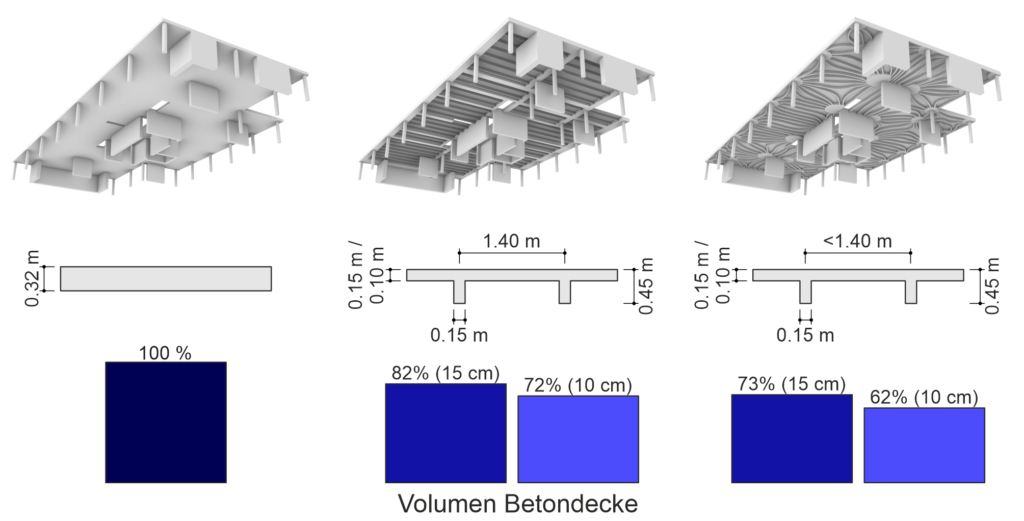
Die Herausforderung besteht nun darin, zuverlässige und effiziente Methoden zu finden, solche oder ähnliche geometrisch komplexen Tragwerke mithilfe von DFB herzustellen. Tatsächlich wurden sowohl an der ETH (im Rahmen des NFS Digitale Fabrikation) als auch weltweit bereits erste Konzepte für digital fabrizierte Betondecken entwickelt – Beispiele hierfür sind in Abbildung 3 ersichtlich. Von den meist aufwendig produzierten Prototypen zu einem massenmarkttauglichen System, welches die Möglichkeiten der digitalen Fertigung voll ausschöpft, ist es jedoch noch ein weiter Weg. Wir wollen dabei einen Beitrag leisten, indem wir Systeme entwickeln, welche DFB nur einsetzt, wo die gewonnene geometrische Freiheit vorteilhaft ist und so die Vorteile von DFB und herkömmlichen Bauverfahren vereinen.
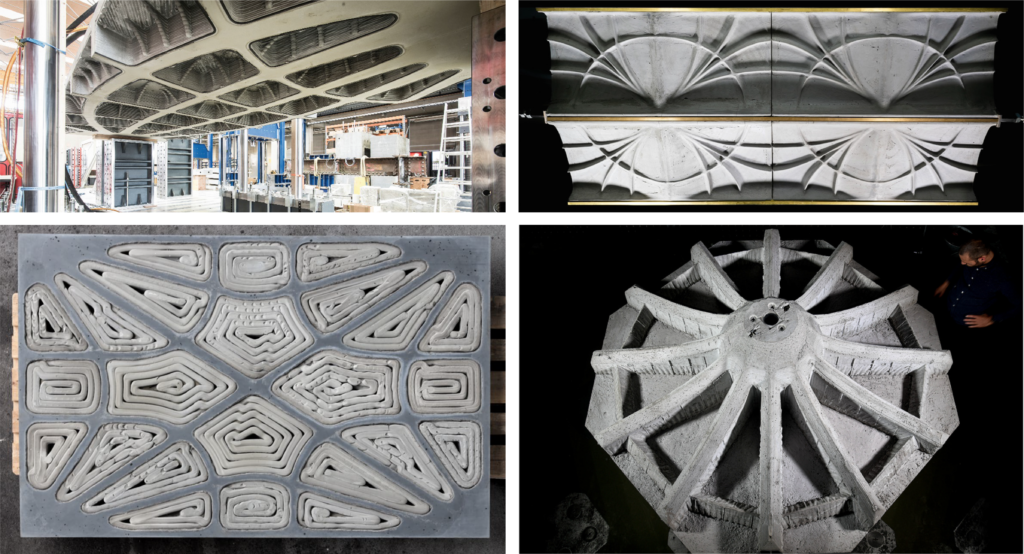
Die Vielfältigkeit der Anforderungen, welche an Decken gestellt werden in Kombination mit den Möglichkeiten und Herausforderungen, welche DFB mit sich bringt, machen dieses Forschungsprojekt zu einer komplexen Aufgabe – es bleibt also spannend und wir freuen uns, hier zu gegebener Zeit über die Fortschritte des Projekts zu informieren.
Rebecca Ammann