Link zur deutschen Version: Der Weg zu nachhaltigeren Betondecken mittels digitaler Fertigung
Greenhouse gas emissions must be drastically reduced in the face of the climate crisis. The building industry, accounting for around 37 per cent of global operational energy- and process-related greenhouse gas emissions, must become more environmentally friendly, especially considering the increasing demand in floor area in the coming years (2022 Global Status Report for Buildings and Construction). A change of mind is necessary at all levels to achieve this reduction in negative environmental impacts. While alternative building materials are currently receiving a great deal of attention in academia and industry, implementing efficient load-bearing structures is an often-underestimated measure with enormous saving potential. (The Institution of Structural Engineers, 2022)
Given that around half of the material in a typical building is used in floor slabs (Bischof et al. 2022), striving for optimisation of material efficiency in these structural elements is evident. In fact, there are numerous tried-and-tested floor slab systems resulting in massively reduced greenhouse gas emissions compared to the widespread flat slabs: By choosing statically efficient structures such as ribbed slabs, waffle slabs or hollow core slabs, up to 60% of greenhouse gas emissions can be saved compared to flat slabs, depending on the span (Regúlez et al., 2022). So why do we still predominantly build flat slabs nowadays?
This question can be answered with a holistic view of the problem: Floor slabs are not or only conditionally chosen because of their greenhouse gas emissions, but rather criteria such as construction costs, construction time, sound insulation, the possibility of integrating building services components and many others are decisive. In other words, floor slabs must be environmentally sustainable (including emissions, resource consumption and waste production, durability and, where appropriate, circularity), socially sustainable (including safety, functionality and adaptability) and economically sustainable (including cost, construction and flexibility) to be suitable for the mass market. Only systems suitable for the mass market can have a lasting positive impact. The complexity of these requirements is summarised in Figure 1.
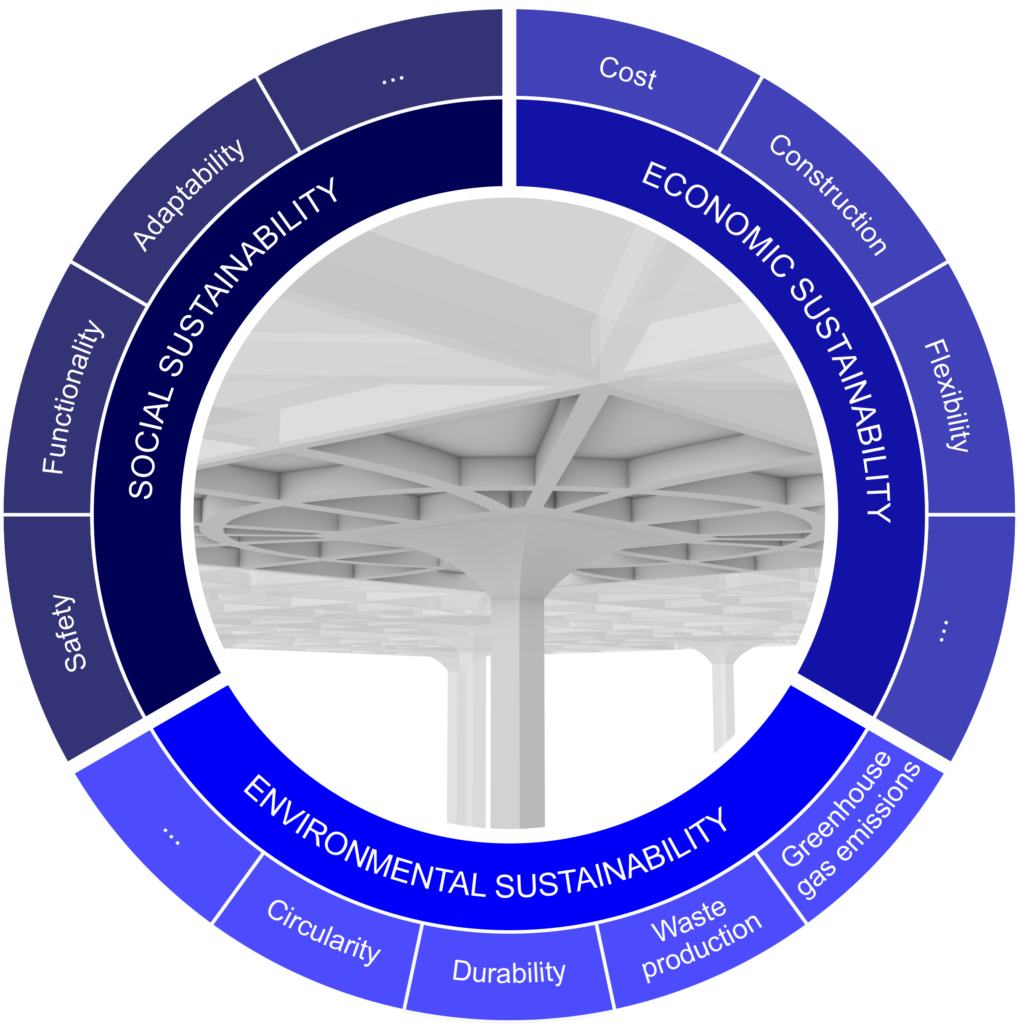
For many of these criteria, choosing a flat slab, whose production has been optimised for decades, is advantageous: Not only are flat slabs inexpensive to build, but they also have a low overall depth and good acoustic sound insulation properties and offer the possibility of integrating building services as inserts. The geometric freedom in the floor plan, made possible by flat slabs, should also not be underestimated: The static efficiency achieved with load-bearing systems such as ribbed slabs often requires cross-sections with greater geometric complexity. Due to the more labour-intensive formwork required, such slabs are generally not produced in situ but are fully or partially prefabricated using reusable formworks. These reusable formworks are generally only suitable for regular and repetitive floor plans, causing a reduction in the geometric freedom of the plan layout. Also, the load transfer in slab systems such as ribbed slabs and hollow core slabs is generally one-way (in comparison with two-way spanning flat slabs), further limiting the geometric freedom in the floor plan.
All these reasons lead to emission-intensive flat slabs being chosen, despite the increased awareness of sustainability in recent years.
The innovative field of digital fabrication with concrete (DFC) could potentially contribute to a more frequent choice of efficient load-bearing systems in the future: Through a variety of fabrication technologies, of which 3D concrete printing (3DCP) is the best-known, the fabrication of geometrically complex, customised structures should be possible without or with minimal formwork, while reducing production costs and increasing worker safety (Wangler et al., 2016). The potential impact of this geometric freedom in practice can be seen in Figure 2: For a floor plan, a flat slab, a ribbed slab with straight, regular ribs and a free-form ribbed slab, as it could be potentially produced with the help of digital manufacturing methods, were pre-dimensioned. Due to the more direct load transfer, the potential material savings with the free-form ribbed floor slab are larger than with the ribbed slab with straight ribs (27% – 38% instead of 18% – 28% reduction in concrete slab volume). Also, there are fewer adjustments to the floor plan (such as additional columns).
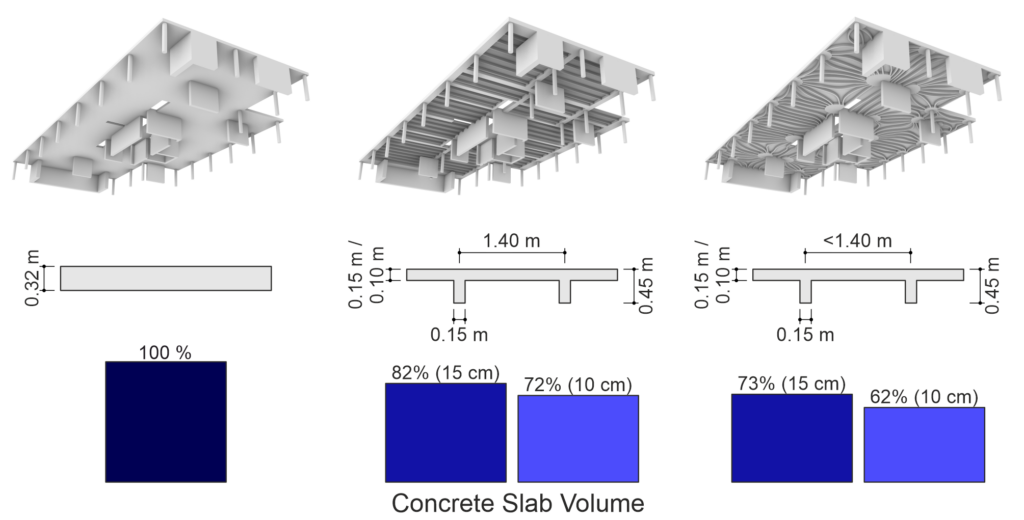
Finding reliable and efficient methods and workflows to produce such or similar geometrically complex structures using DFC is key. In fact, the first concepts for digitally fabricated concrete floors have already been developed both at ETH (within the NCCR Digital Fabrication) and worldwide (see Figure 3). However, it is still a long way from these prototypes, often requiring enormous amounts of manual labour, to a system suitable for the mass market that exploits the possibilities of digital fabrication. We want to proceed along this path by developing systems that use DFC only where the geometric freedom gained is beneficial, thus combining the advantages of DFB and conventional construction methods.
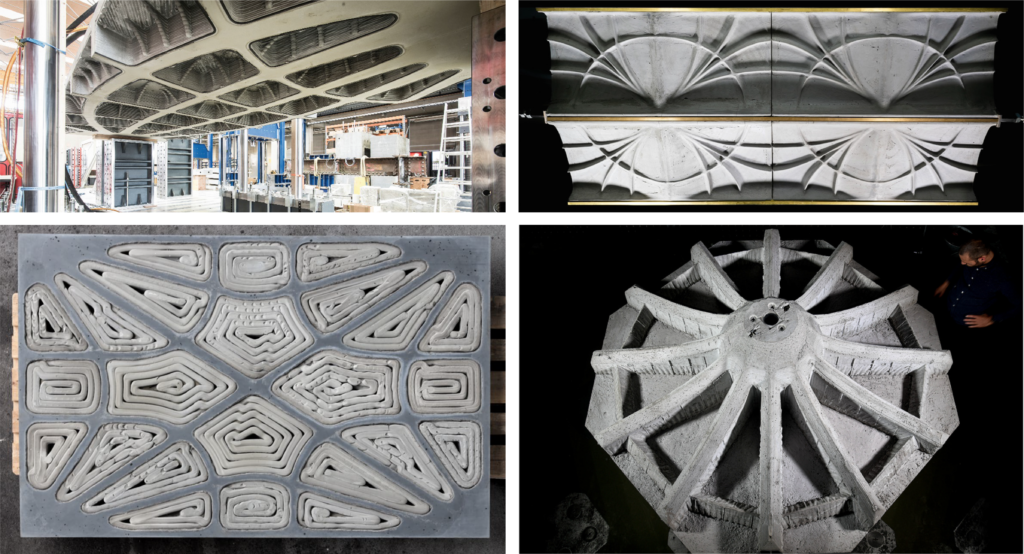
The variety of requirements floor slabs need to fulfil, combined with the possibilities and challenges that DFC entails, make this research project a complex and exciting task – we look forward to updating you about the project’s progress in due course.
Rebecca Ammann