Link zur deutschen Version: Der Weg zur automatischen Rissmessung in Versuchen zum Tragverhalten von Beton.
Almost five years ago, as part of a Master’s project thesis, I received the opportunity to develop first methods for a crack measurement tool for the evaluation of concrete tests. The aim was to automatically detect cracks and measure their width and slip from the surface deformation measurements obtained by digital image correlation. My supervisors Prof. Dr. Walter Kaufmann and Dr. Jaime Mata-Falcón had already worked out the first ideas and concepts at this point and some test data were also available. After completing the project thesis, the tool was continuously refined and increasingly used in the analysis of our experiments. The procedure showed great potential, so that today it is freely available as open-source software under the name ACDM (for “automated crack detection and measurement”). The graphical user interface allows an easy application and also other research institutes have started using this tool. This blog post is about the process leading to today’s ACDM, its importance in experimental research and the most important elements that helped the tool to leverage.
Why are crack measurements in experiments so important?
To better understand the load-bearing behaviour of concrete elements and to be able to develop and validate models, structural tests are necessary for which the cracking behaviour is accurately assessed. For example, the shear force that can be transmitted across cracks due to aggregate interlock is strongly dependent on the roughness of the crack surface and the crack width. Such properties must be recorded accurately in order to allow validating aggregate interlock models. In many cases, large-scale tests are required to obtain results that are representative of real-life structures. However, such large-scale tests are very laborious and generally show a complex crack pattern, where the exact crack locations cannot be predicted. Various instrumentation techniques have already been developed for measuring cracks, but their applicability is often severely limited. This is mainly because the resolution and accuracy of the measured crack kinematics, i.e., crack width and sliding, are usually not sufficient to assess the actual load-bearing and deformation behaviour of the material reliably. The accurate measurement of cracks with a high resolution is therefore crucial but is a major challenge.
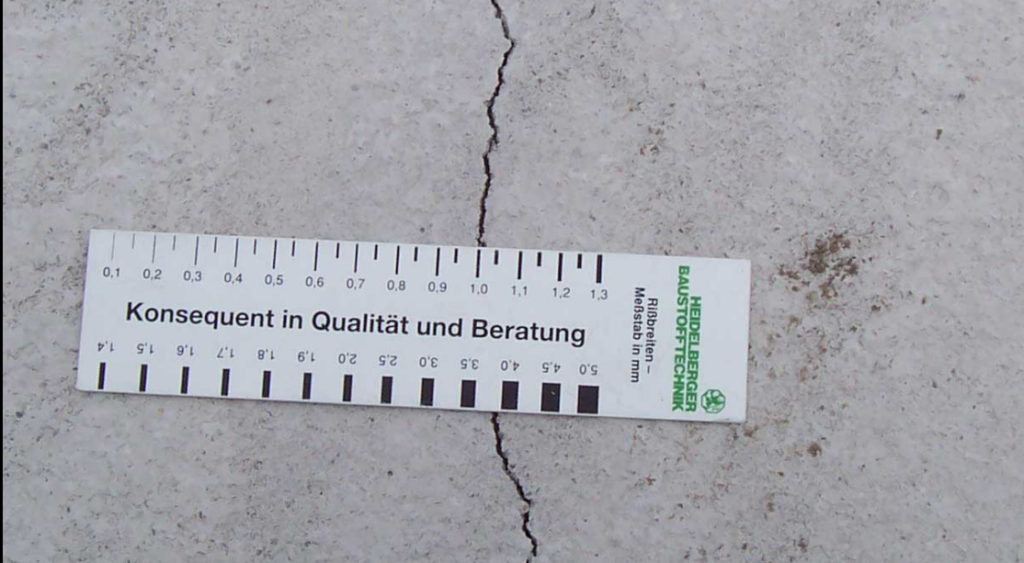
How have cracks been measured in the past?
Until some time ago, the standard procedure for measuring cracks in experiments consisted of temporarily stopping the experiment at selected load or deformation states and measuring relevant crack widths by hand using crack rulers or crack magnifiers directly on the surface of the specimen. However, this manual measurement method is prone to measurement errors and is also very time-consuming, especially for large-scale tests with a large number of cracks. Furthermore, for elements with low deformation capacity, relevant measurements close to the failure are usually missing due to the risk involved in terms of safety for the personnel.
Alternative measurement techniques – such as the use of DEMEC, NDI or LVDTs (“linear variable differential transformers“) – improve the accuracy of crack measurements as well as the temporal resolution, but are still limited to a few predefined crack locations and therefore hardly applicable to complex crack patterns where the exact crack locations usually cannot be predicted.
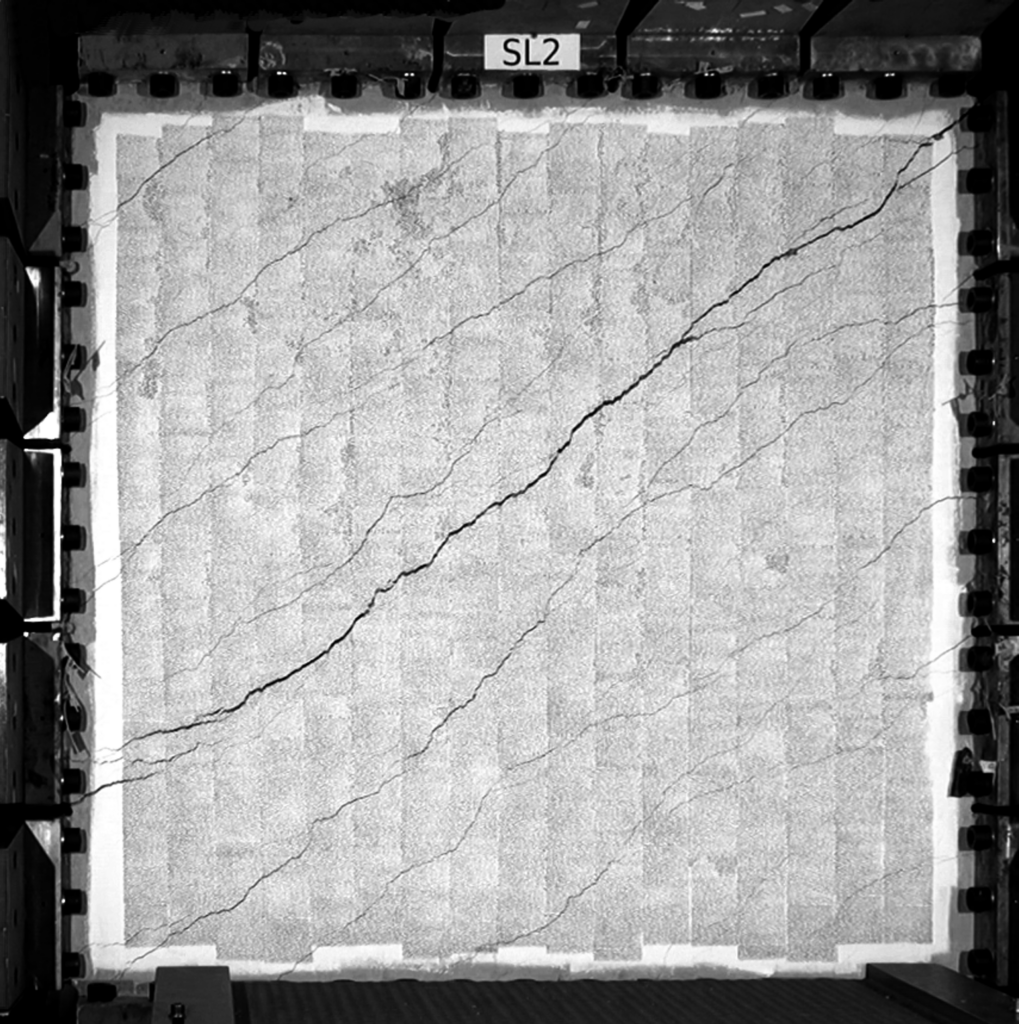
What are the benefits of digital image correlation (DIC)?
Digital image correlation (DIC) is a camera-based deformation measurement method for surfaces in which the deformation of a pattern consisting of random points is measured by correlation algorithms. From the full-field and high-precision displacement measurements obtained in this way, surface strains of the component can also be calculated using relatively simple procedures. Compared to conventional measurement methods, DIC provides quasi-continuous measurements (spatially and temporally), and thus offers new possibilities for very detailed and reliable assessment of the crack behaviour in laboratory tests.
Although DIC is already used in many research institutions to measure crack openings and slidings, the results are usually only determined at a few discrete points using manually set extensometers, which means that much valuable information is lost. Such manual procedures are also hardly applicable to large-scale tests with complex crack patterns. The DIC data volumes generated in large-scale tests are extremely large and can therefore only be efficiently processed into usable results by automatic procedures. In addition, the crack openings and slidings must be determined through virtual reference points that are somewhat separated from the actual crack line in order to obtain bias-free measurements. This leads to the fact that even slight rotations of the specimen have to be taken into account (especially for crack slip measurements), which considerably complicates the procedure. However, it must be mentioned here that the latter point applies to all crack measurement methods in which crack lip displacements are not measured directly but through reference points that are just slightly separated from the crack line (hence, also for crack measurements using manual DIC extensometers but also e.g. when using DEMEC, NDI or LVDTs).
Concept of displacement measurements based on DIC. DIC setup in the Large Universal Shell Element Tester (LUSET) with two cameras to measure 3D displacements. Image credits: Mata Falcón et al. 2020.
To use DIC efficiently for assessing the crack behaviour in concrete tests – which would not be possible with this accuracy and resolution by other known instrumentation techniques – first steps towards today’s fully automated DIC-based crack detection and measurement tool “ACDM” were taken in our research group some years ago.
What have been the first steps in the development of ACDM?
From the beginning, the basic concept of ACDM was to use the relationship that the local surface tensile strain at cracks theoretically becomes infinitely large. However, due to the finite resolution of the DIC and the fact that the strain field is often filtered to reduce the measurement noise, finite tensile strains result at the cracks. The size of the calculated principal tensile strain is then related to the crack kinematics, i.e. the crack openings (deformation perpendicular to the crack inclination) and the crack sliding (deformation parallel to the crack inclination). Thus, we sought a method to extract cracks at locations with high principal tensile strains. A first solution was to determine zones with high strains and then thin them into crack lines (as crack skeleton) by well-established morphological operations.
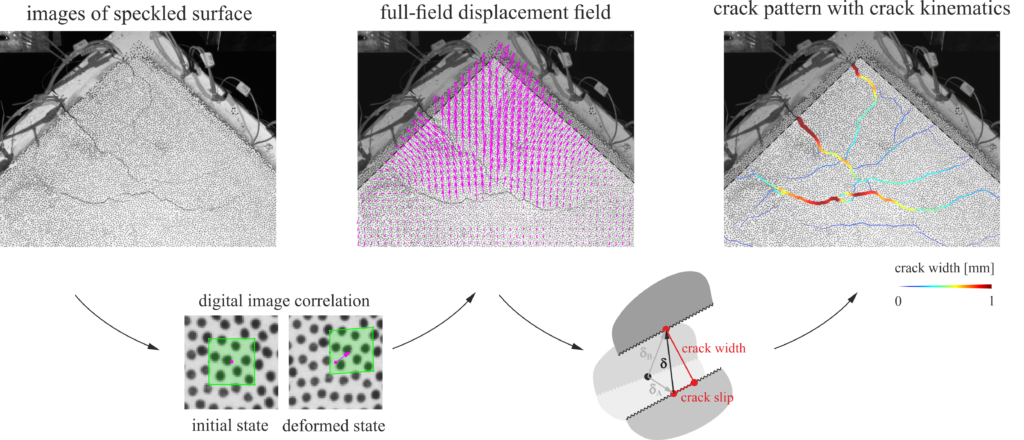
The detected crack lines have the great advantage over individual independent crack points that the local crack inclination can be calculated for each crack point, which is needed, among others, to determine the crack kinematics. The crack lip displacements were calculated in a first step using two reference points (at each side of the crack) in order that – as already mentioned – local rotations of the specimen could be taken into account.
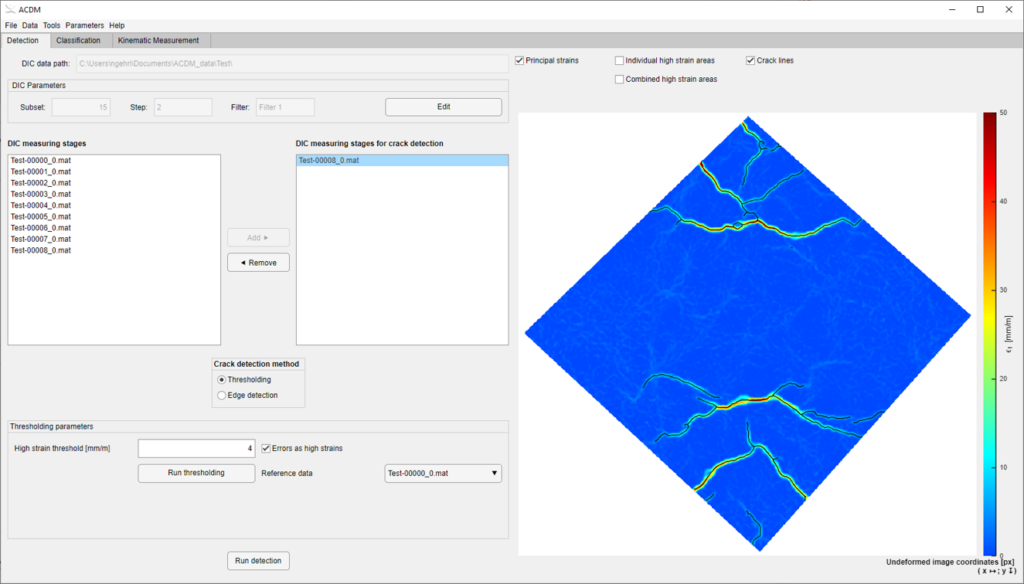
How was ACDM refined into a fully automated software?
From the beginning, the methods were integrated into a graphical user interface to facilitate the use of the tool. In tests with a relatively simple crack pattern, it quickly became apparent that ACDM provides very accurate results of crack locations and crack kinematics. For more complex crack patterns, however, problems with biased results in areas close to crack intersections were observed, where the method failed. Therefore, in a next step, the crack detection procedure was revised. Instead of zones with high strains being thinned to crack lines, in today’s version of ACDM the crack lines are extracted directly as edges in the strain field. In addition, the number of reference points was increased in the calculation of crack kinematics and an algorithm was developed that improves the reliability of the results.
ACDM is available to the public as open-source software at https://gitlab.ethz.ch/ibk-kfm-public/acdm. In various experiments of our research group and especially in our large-scale tests in the Large Universal Shell Element Tester (LUSET), ACDM has already been successfully applied and could thus contribute to relevant new findings on the load-bearing behaviour of concrete. For example, Alexander Beck and Demis Karagiannis tested 2.0 x 2.0 large-scale concrete panels in LUSET as part of their recently published doctoral theses, using ACDM in the evaluation of the test results. The obtained information on the crack behaviour was of central importance in the development and validation of their mechanical models. But ACDM also found favour outside ETH and has already been used in various studies to evaluate experiments.
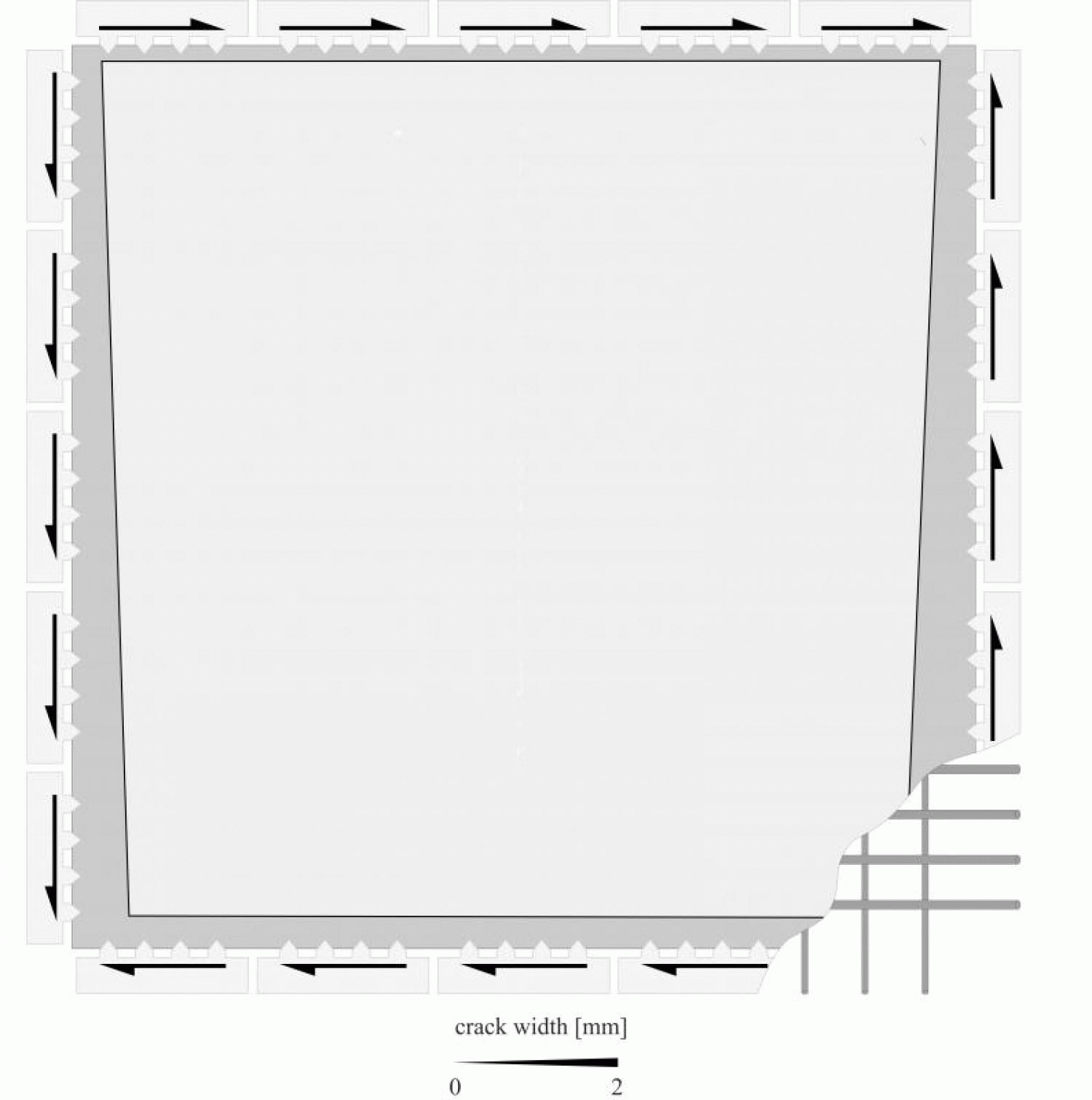
rack pattern of a panel test in LUSET subjected to combined shear and bending loads. Image credits: Karagiannis 2021. Crack pattern of a shear panel test in LUSET. Image credits: Beck 2021.
To ensure that this continues in the future, we are constantly improving ACDM. One goal we have been pursuing for a long time, for example, is the real-time measurement of cracks using ACDM, which would enable us to conduct experiments by controlling crack widths or crack slidings (which, for instance, is important in experiments with fibre reinforced concrete elements). We also see potential of ACDM in monitoring of existing structures for early damage detection. Corresponding investigations are currently being carried out.
Nicola Gehri