Link zur deutschen Version: Schalung als zentrale Herausforderung bei der Herstellung von effizienten, wirtschaftlichen und nachhaltigen Betondecken
The current environmental crisis urges the construction of more sustainable structures, which requires a radical change in the way we design and build nowadays [1]. Although changes in the construction industry are traditionally slow compared to other industries, such as the automotive or computer industry, there is already (at least) a general agreement in academia about the urge to reduce, reuse, recycle and recover construction materials and structures in order to achieve a radical drop in the CO2 emissions from an industry responsible of 38% of the global greenhouse gas emissions [2][3].
Research groups are making considerable efforts to address the structural and fabrication optimisation of concrete slabs seeking a reduction in material consumption, as these elements generally take between 40 % and 60 % of the concrete in the building’s structure [4]. Furthermore, lighter slabs would transmit lower loads to the vertical structure resulting in smaller dimensions of pillars, walls and foundations.
Structural efficiency is sought through shape, topology and size optimisation, resulting in thin-shell flooring systems of different kinds [5][6], ribbed slabs [7][8] or the combination of both [9][10][11]. Cutting-edge methods and software allow concrete floor models with a maximum degree of structural optimisation. Although innovative uses of digital fabrication are being used, the construction of these usually-complex shapes still presents several difficulties regarding sustainability and economy. While the former requirement is usually self-imposed until stronger sustainability regulations are established, the crude reality of the construction industry reminds researchers who want to spread out their innovations that a system which is not economically profitable has very few chances to enter the mass market and, therefore, have an impact on the society. One of the major challenges concerning these issues is related to the fabrication of the formwork.*
A look into the past can clarify the importance of economic formwork to build non-straight elements, mainly vaults and shells. Ancient, great master builders, architects or engineers relied on a specific economic way to fabricate or use the formwork to be able to build their masonry or concrete shells, or, in some cases, they even resorted to techniques which did not require any formwork. Some examples of the many existing ones are featured in the following paragraphs.
After emigrating from Spain in 1881, the Guastavinos (Rafael Guastavino Sr. and his son) built around 1000 buildings in the United States thanks to an economic, expressive and fire-proof construction technique: tile vaulting [12]. Tile vaults (sometimes referred to as thin-tile, timbrel, Catalan or Guastavino vaults) are masonry structures made with thin bricks (tiles), mortar and fast-setting cement or gypsum. The bricks are placed flat, building up to two, three or more courses. Traditionally, tiles are used because of their lightweight, which is a necessary condition, together with the use of a fast-setting binder, to build the first course without supporting formwork [13] [14] [15] (Figure 1).

The engineer Eduardo Torroja (1899-1961) also used this construction technique because “such shells [tile vaults] are cheap to make and may be adapted to any desired shape, even to continuously changing curvatures, […]. If constructed by bricklayers skilled in the technique, they can be made without the aid of formwork.” [16]. He used it in combination with reinforcement in, for example, a church in Pont de Suert (Figure 2) or the foundations of the Sancti Petri Bridge in Cadiz, both in Spain [17] [18] [19].
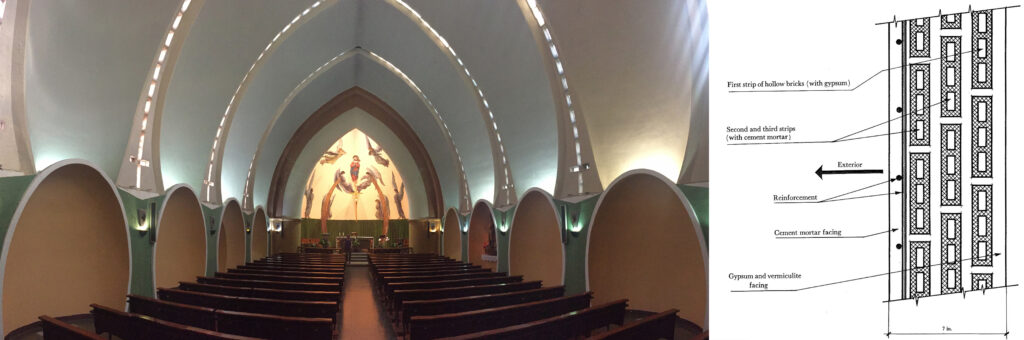
The Italian engineer Pier Luigi Nervi (1891-1979) also made big efforts to achieve economic construction techniques through appropriate formwork systems. Seeking to avoid the massive timber formwork that he used in some of his first hangars for the Italian Air Force, his search led him to the use of prefabricated concrete elements and ferrocement reusable formwork on moveable scaffoldings [20].
Reusable and moveable formworks were also used by the Uruguayan engineer Eladio Dieste (1917-2000) [21]. This fact has an extraordinary impact on the design of his reinforced brick shells, which feature a repetitive rhythm of the same shape along the length of the building (Figure 3). The amount and type of mortar in the bricks’ joints allowed a quick removal of the formwork to be used as soon as possible for the next part of the building [22] [23].
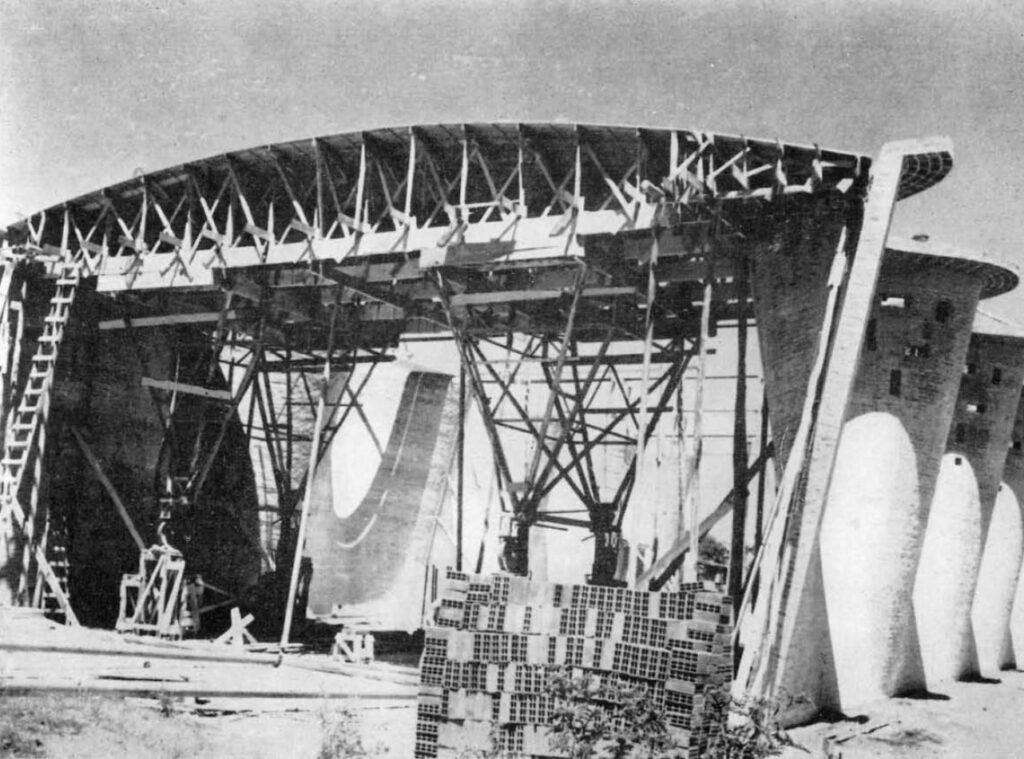
The Spanish architect Félix Candela (1910-1997) achieved economic formworks for his concrete shells by shaping his structures as hyperbolic paraboloids. Such ruled surfaces allowed easy and fast construction of the formwork using only reusable, straight, wooden planks. This system, together with the relatively low labour cost at that time and location, allowed him to have a prolific career building concrete thin-shell structures [25].
Hyperbolic paraboloids were also built by Antoni Gaudí (1852-1926) and Luis Moya (1904-1990) using the tile vaulting technique. Gaudí would use this shape for the tile vaults at the porch of the Colonia Güell’s church in Santa Coloma de Cervelló, Spain [26]. He would then pour concrete on the tile-vaulted integrated formwork to create a hybrid masonry-concrete structure [19]. In the case of the architect Luis Moya, a hyperbolic paraboloid was used to cover the chapel that he designed for the School Santa María del Pilar in Madrid, Spain [27]. This roof is a 743 m2, 14-cm-thick, reinforced tile vault built using a falsework of wooden planks with a separation of 60 cm. Reinforcement is placed in between the courses of bricks while a 10-cm layer of light concrete is applied on top of the masonry [28] (Figure 4).
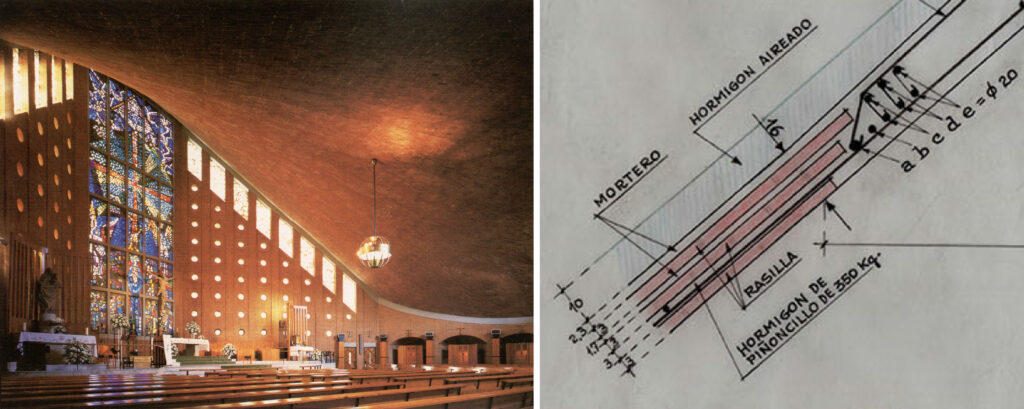
The use of tile vaults as integrated formwork for concrete is a possibility explored by the author of these lines [29]. The research on this topic presents this construction technique as a possible way to build expressive, reinforced concrete shells (including floor systems) using tile vaults as integrated formwork, aiming at reducing costs and material waste while providing a unique finishing at the intrados [30] (Figure 5). The construction costs can be reduced mainly due to the low cost of the materials involved and the fact that no additional formwork or related foundations are needed.
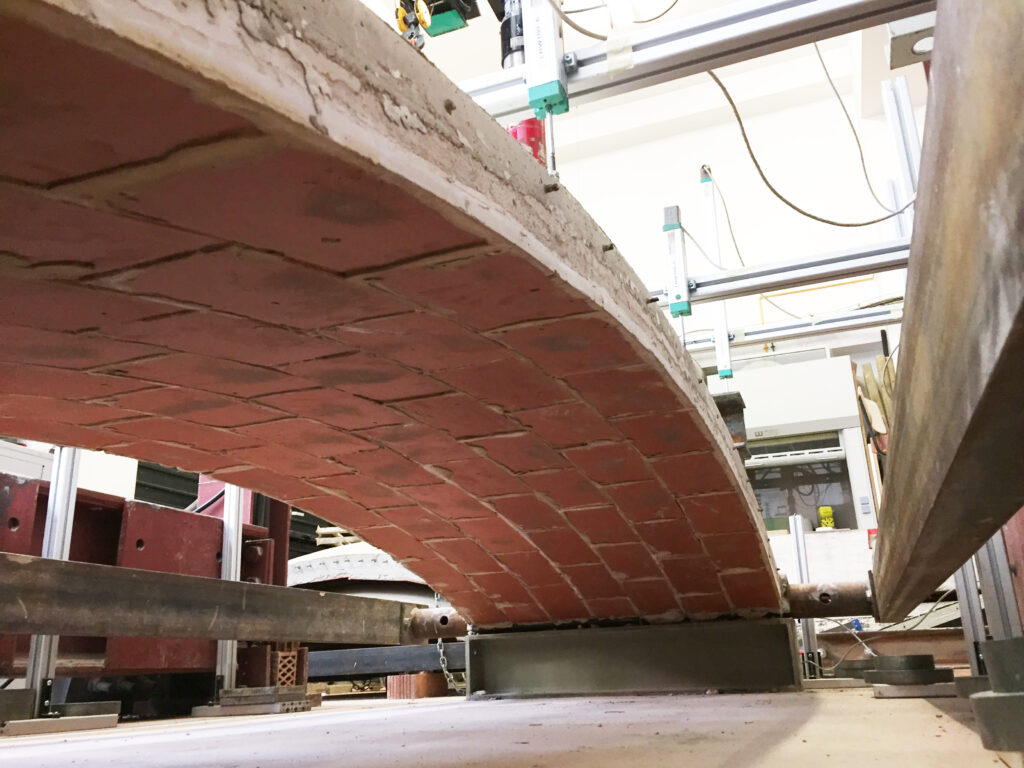
Experimental research, including load tests on material samples and full-scale prototypes, was carried out to validate the construction technique, being the first laboratory tests of this kind of composite structures [31] [32] (Figure 6). The calibration of finite element models based on the experimental results allowed the definition of a reliable modelling technique, material model and material properties for the analysis of this kind of structures. Additionally, a method based on limit analysis [33] was described to safely design such singly-curved structures and assess their strength and stability against external loading. The method was called Extended Limit Analysis of Reinforced Masonry (ELARM), started by Roca et al. [34] and provides graphical and intuitive results in 2D [30]. A three-dimensional approach of ELARM was presented as well [35].
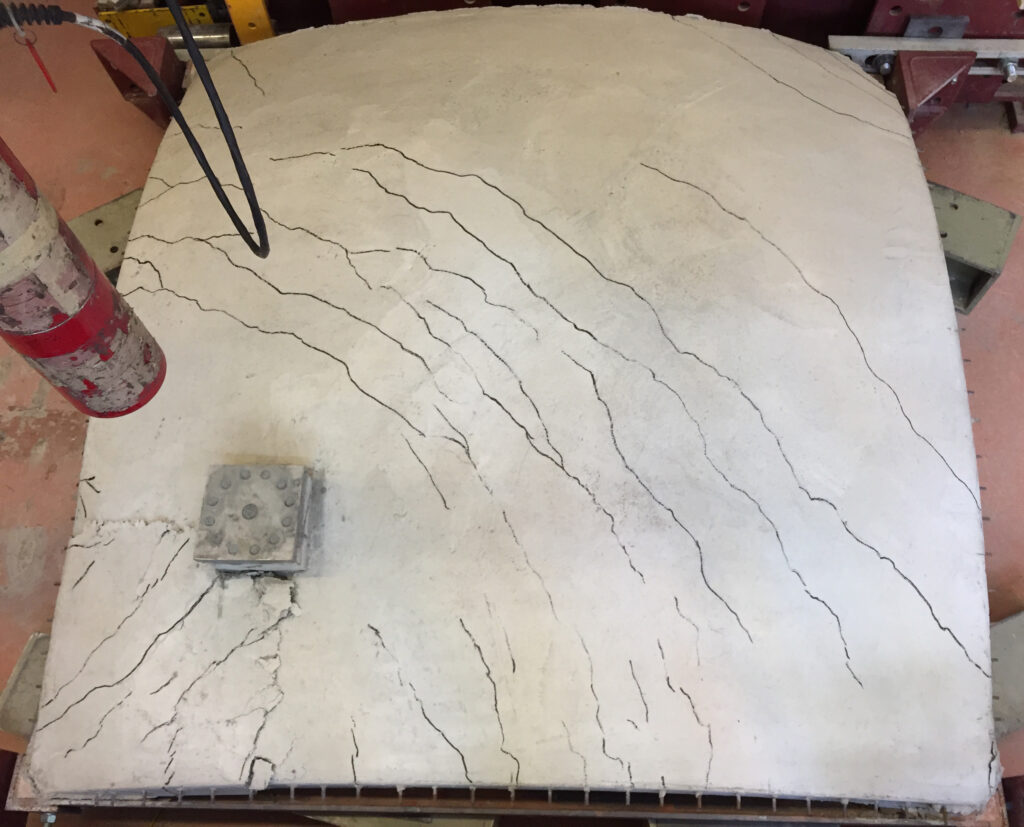
Structural analysis, experimental research and design methods have been successfully provided for this construction technique. However, this is not enough to make it enter the construction mass market. The assessment of the technique’s viability is highly dependent on the shape, the span and the number of times this shape is repeated. Moreover, construction costs are variable and depend on many factors, the location being an important one. Regarding the main topic of this post, i.e., considering the use of the presented technique for small- or medium-span floor systems, it could be profitable and competitive in contexts where the construction labour force is not expensive.
Finding the balance between sustainability and economy in the fabrication of optimised floor slabs is one of the challenges of the third phase of the ETH-based National Centre of Competence in Research Digital Fabrication (NCCR dfab). On the one hand, researchers need to address sustainability focused on material and waste reduction, the use of materials with less carbon footprint, circular construction and reuse possibilities. On the other hand, economic systems should be created to allow the developed ideas, concepts and patents to get to the mass market to represent a fundamental change in the construction industry.
As mentioned above, solutions are context-dependent. Local resources, materials, traditions and know-how make a system succeed or fail in different parts of the world. Therefore, to achieve a relevant, global environmental impact, special attention should be paid to the implementation of innovations where extensive construction will happen in the following decades.
*In this post, the term “formwork” in parts also refers to the elements supporting the formwork in the sense of “falsework”.
[1] Block P, Van Mele T, Rippmann M, Ranaudo F, Calvo Barentin C, Paulson N. Redefining Structural Art: Strategies, necessities and opportunities. The Structural Engineer 2020;98:66–72.
[2] Mai I, Brohmann L, Freund N, Gantner S, Kloft H, Lowke D, et al. Large Particle 3D Concrete Printing—A Green and Viable Solution. Materials 2021;14:6125. https://doi.org/10.3390/ma14206125.
[3] Agustí-Juan I, Habert G. Environmental design guidelines for digital fabrication. Journal of Cleaner Production 2017;142:2780–91. https://doi.org/10.1016/j.jclepro.2016.10.190.
[4] Bischof P, Mata-Falcón J, Kaufmann W. Fostering innovative and sustainable mass-market construction using digital fabrication with concrete. Cement and Concrete Research 2022;161:106948. https://doi.org/10.1016/j.cemconres.2022.106948.
[5] Hawkins W, Orr J, Shepherd P, Ibell T. Design, Construction and Testing of a Low Carbon Thin-Shell Concrete Flooring System. Structures 2019;18:60–71. https://doi.org/10.1016/j.istruc.2018.10.006.
[6] Hawkins W, Orr J, Ibell T, Shepherd P. A design methodology to reduce the embodied carbon of concrete buildings using thin-shell floors. Engineering Structures 2020;207:110195. https://doi.org/10.1016/j.engstruct.2020.110195.
[7] Mata-Falcón J, Bischof P, Huber T, Anton A, Burger J, Ranaudo F, et al. Digitally fabricated ribbed concrete floor slabs: a sustainable solution for construction. RILEM Tech Lett 2022;7:68–78. https://doi.org/10.21809/rilemtechlett.2022.161.
[8] Burger J, Huber T, Mata-Falcón J, Lloret Fritschi E, Kaufmann W, Gramazio F, et al. Design, fabrication, and testing of an optimised reinforced concrete floor slab fabricated with robotically 3D printed formwork (accepted). Third RILEM International Conference on Concrete and Digital Fabrication, 2022.
[9] López López D, Veenendaal D, Akbarzadeh M, Block P. Prototype of an ultra-thin, concrete vaulted floor system. Proceedings of IASS Annual Symposia 2014;2014:1–8.
[10] Liew A, López López D, Van Mele T, Block P. Design, fabrication and testing of a prototype, thin-vaulted, unreinforced concrete floor. Engineering Structures 2017;137:323–35. https://doi.org/10.1016/j.engstruct.2017.01.075.
[11] Nuh M, Oval R, Orr J, Shepherd P. Digital fabrication of ribbed concrete shells using automated robotic concrete spraying. Additive Manufacturing 2022:103159. https://doi.org/10.1016/j.addma.2022.103159.
[12] Ochsendorf J. Guastavino Vaulting: The Art of Structural Tile. Reprint edition. New York: Princeton Architectural Press; 2013.
[13] Truñó A. Construcción de bóvedas tabicadas. 1st edition. Madrid: INSTITUTO JUAN DE HERRERA; 2004.
[14] López López D, Domènech Rodríguez M, Palumbo Fernández M. “Brick-topia”, the thin-tile vaulted pavilion. Case Studies in Structural Engineering 2014;2:33–40. https://doi.org/10.1016/j.csse.2014.09.001.
[15] López López D, Van Mele T, Block P. Tile vaulting in the 21st century. Informes de la Construcción 2016;68:e162–e162. https://doi.org/10.3989/ic.15.169.m15.
[16] Torroja Miret E. The structures of Eduardo Torroja: an autobiography of engineering accomplishment. New York: F.W. Dodge Corporation; 1958.
[17] Torroja Miret E. Memoria. No 19.301 1926.
[18] Torroja Miret E. Iglesia de Pont de Suert. Informes de la Construcción 1962;14:59–70. https://doi.org/10.3989/ic.1962.v14.i137.4933.
[19] López López D, Van Mele T, Block P. The combination of tile vaults with reinforcement and concrete. International Journal of Architectural Heritage 2019;13:782–98. https://doi.org/10.1080/15583058.2018.1476606.
[20] Halpern AB, Billington DP, Adriaenssens S. The Ribbed Floor Slab Systems of Pier Luigi Nervi n.d.:7.
[21] Anderson S. Eladio Dieste: Innovation in Structural Art. 1st edition. New York: Princeton Architectural Press; 2004.
[22] Dieste E, Arana M, Garabelli L. Diálogos con Dieste. SUMMA 1980;8:96–101.
[23] López López D, Van Mele T, Block P. Dieste, González Zuleta and Sánchez del Río: Three approaches to reinforced-brick shell structures. Structural Analysis of Historical Constructions: Anamnesis, Diagnosis, Therapy, Controls, CRC Press; 2016.
[24] Dieste E. Iglesia en Montevideo. Templo parroquial de Atlántida. Informes de la Construcción 1961;13:43–56. https://doi.org/10.3989/ic.1961.v13.i127.5106.
[25] Cassinello P, Schlaich M, Torroja JA. Félix Candela. In memorian (1910-1997). From thin concrete shells to the 21st century’s lightweight structures. Informes de la Construcción 2010;62:5–26. https://doi.org/10.3989/ic.10.040.
[26] González Moreno-Navarro JL, Casals Balagué A. Gaudí y la razón constructiva. Un legado inagotable. Akal; 2002.
[27] Moya Blanco L, Domínguez Salazar JA. Capilla del Colegio de Santa María del Pilar, Madrid. Informes de la Construcción 1965;18:49–61. https://doi.org/10.3989/ic.1965.v18.i173.4340.
[28] Moya Blanco L. Memoria descriptiva de construcción y material y mediciones del proyecto para la construcción de una capilla y cripta en el colegio Santa María del Pilar 1963.
[29] López López D. Tile Vaults as Integrated Formwork for Concrete Shells: Construction, Experimental Testing, Structural Analysis and Design. Doctoral Thesis. ETH Zurich, 2019. https://doi.org/10.3929/ethz-b-000417993.
[30] López López D, Roca P, Liew A, Van Mele T, Block P. Tile vaults as integrated formwork for reinforced concrete: Construction, experimental testing and a method for the design and analysis of two-dimensional structures. Engineering Structures 2019;188:233–48. https://doi.org/10.1016/j.engstruct.2019.03.034.
[31] López López D, Bernat-Maso E, Gil L, Roca P. Experimental testing of a composite structural system using tile vaults as integrated formwork for reinforced concrete. Construction and Building Materials 2021;300:123974. https://doi.org/10.1016/j.conbuildmat.2021.123974.
[32] López López D, Bernat-Maso E, Gil L, Roca P. Experimental testing of tile vaults. Brick and Block Masonry – From Historical to Sustainable Masonry, CRC Press; 2020.
[33] Heyman J. The stone skeleton. International Journal of Solids and Structures 1966;2:249–79.
[34] Roca P, López-Almansa F, Miquel J, Hanganu A. Limit analysis of reinforced masonry vaults. Engineering Structures 2007;29:431–9. https://doi.org/10.1016/j.engstruct.2006.05.009.
[35] López López D, Roca P, Liew A, Méndez Echenagucia T, Van Mele T, Block P. A three-dimensional approach to the Extended Limit Analysis of Reinforced Masonry. Structures 2022;35:1062–77. https://doi.org/10.1016/j.istruc.2021.06.013.
David López López
Comment on this post on LinkedIn or Instagram