Link zur deutschen Version: Über das Aufkommen von digitaler Fertigung mit Beton
Digital fabrication with concrete (DFC) has emerged as a new trend in the construction industry over recent years. But where does this trend come from, and what is DFC? In this blog contribution, we want to introduce you to the topic of DFC and address the most pressing questions in this field.
What is Digital Fabrication with Concrete?
Digital Fabrication with Concrete describes various fabrication methods where concrete elements are produced in an automated process. With these technologies, almost any type of concrete element can be produced without or with limited formwork and optimised for material usage (Wangler et al. 2019). Therefore, these new processes claim to make the construction industry more efficient and reduce its negative environmental impact. From the various processes that exist, 3D concrete printing (3DCP) is the most widely applied. In 3DCP, a concrete element is produced by adding layers on top of each other, just like in conventional plastic 3D printers.
What’s the history behind these new technologies?
The first automated and layered production of a concrete structure dates back to the 1940s. The Urschel Wall Building Machine was used to build a circular concrete structure with an automated system.
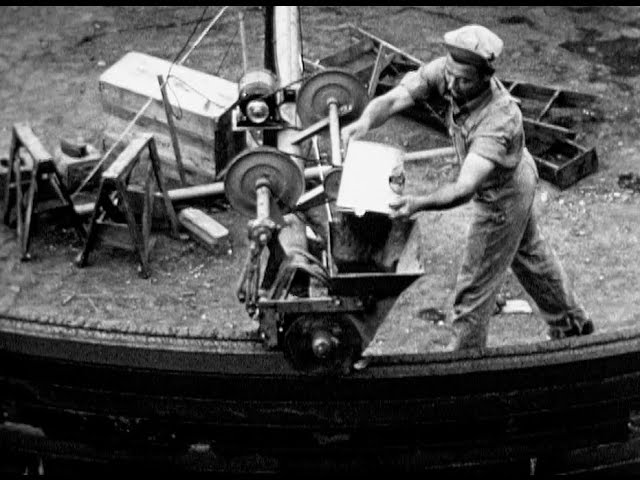
After the first emergence, not much development could be observed in the following decades. In the early 2000s, Prof. Khoshnevis (Khoshnevis 2004) published his work on contour crafting and set off a surge in research and development in 3DCP and other DFC technologies. Today, companies and institutions are using and researching these new technologies all around the world. The most prominent applications are the construction of entire buildings, such as a residential house recently constructed in Germany. Various DFC technologies were used to fabricate the DFAB Housing unit at the NEST building at EMPA. The application of DFC is, however, not only limited to houses. A wide range of applications can be found in various areas such as artistic installations, bridges, infrastructure elements, etc. (see figure below).
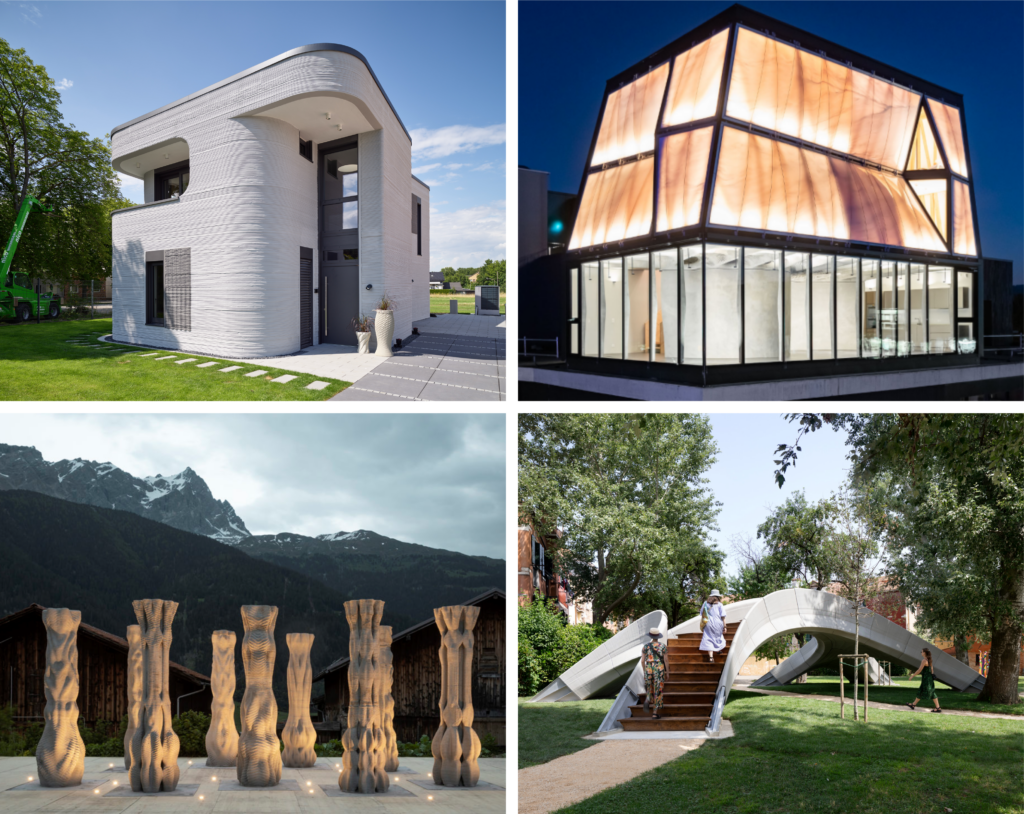
What are the current challenges?
The advancement of DFC technologies, especially 3DCP, faces various challenges. Researchers and builders worldwide are rushing to address these challenges. The main research areas cover material, architectural and structural considerations. On the material level, the fresh and hardened properties, the material composition, and the processing are some of the main areas of interest. For architects, new opportunities and limitations for design arise. The entire building catalogue, including the building systems, can be rethought if DFC is used.
One of the main challenges (and the focus of the author’s research) is the structural application of DFC. Due to the lack of reinforcement approaches, to date, most projects use printed concrete as masonry or as a lost formwork (i.e. to cast a conventional reinforced concrete element inside the printed shell). However, it is questionable if 3D printed concrete (typically with high clinker content) used as masonry or lost formwork leads to more sustainable construction.
Therefore, the range of DFC elements should be expanded into load-bearing applications similar or equal to conventional reinforced concrete to have a lasting positive impact on the construction industry. Therefore, new reinforcement strategies are needed. However, the addition of reinforcement to DFC and especially 3DCP is not straightforward. Without reinforcement, DFC structures designed according to today’s standards can only be used if only compressive stresses occur, no load-bearing requirements exist, or tests verify the structural performance. Accordingly, there is no framework suitable for the mass market telling us how to reliably design and build DFC structures. All these challenges need to be addressed while at the same time keeping general considerations such as socio-economic impacts and sustainability in mind. More details on the current challenges for digital fabrication with concrete are addressed in various review papers such as (Wangler et al. 2019), (Khan et al. 2020) and (Menna et al. 2020).
What is going on at ETH Zurich?
In the year 2014, the NCCR Digital Fabrication funded by the SNSF was initiated. It is a swiss wide “initiative to lead the development and integration of digital technologies within the fields of architecture and construction” (dfab.ch). The project is divided into different research areas addressing different aspects of the digitalisation of the construction industry. One of the research areas focuses on DFC. Within this area, various technologies such as Smart Dynamic Casting (Lloret Fritischi 2016), Eggshell (Burger et al. 2020), Mesh Mould (Hack 2018), KnitCrete (Popescu 2019) and 3DCP (Anton et al. 2020) are being studied in an interdisciplinary manner (see figure below).
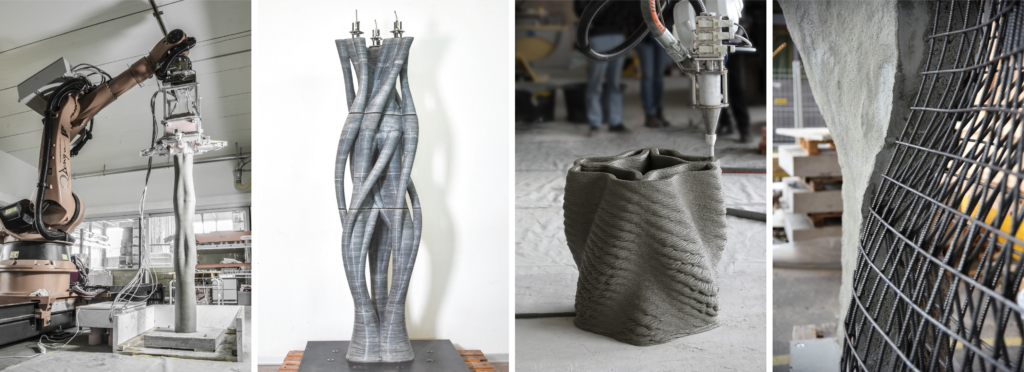
The Chair of Concrete Structures and Bridge Design focuses on the structural aspects of these new technologies. We ask ourselves, how can we build structurally sound elements? How can we create a win-win situation in the combination of reinforcement with DFC processes? Are there reinforcement approaches that could not establish themselves in conventional reinforced concrete but could have new opportunities in the field of DFC? How will we connect the elements, and how are the loads transferred?
With a team of doctoral students and PostDocs, we address these questions by producing structural elements, testing them in our laboratories and, if necessary, adjusting existing models or developing new ones. The figure below shows some examples from our current studies.
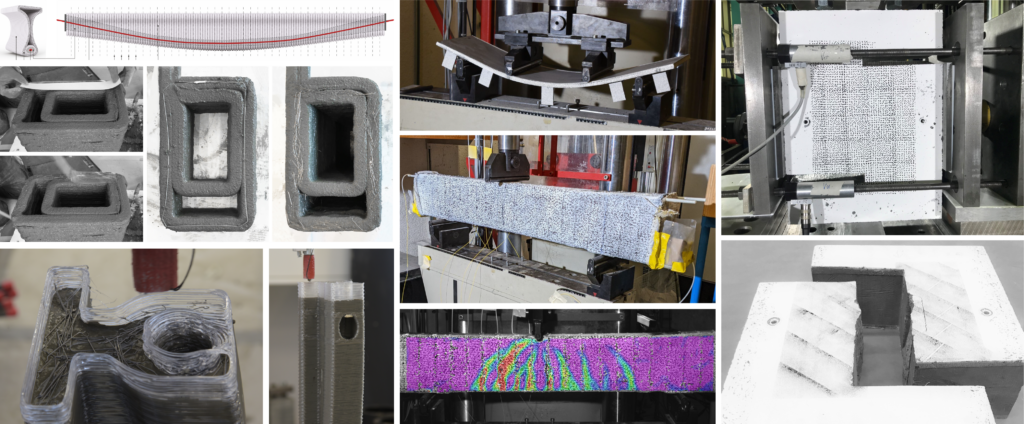
What’s next?
The dreams for DFC technologies are big. From printing multistory buildings up to colonies on Mars. However, DFC technologies are still in a nascent stage. Many limitations still need to be overcome before DFC becomes a main part of the construction industry. The construction industry faces some major challenges in the coming decades. DFC is an exciting area of research that will play a role in providing solutions, but how large of a role remains to be seen.
Lukas Gebhard
Comment this post on LinkedIn or Instagram