Link zur deutschen Version: Entwicklung eines Brückensystems aus CFK-vorgespanntem UHB für die SBB
When looking for a system solution for railway bridges with short spans, e.g. flyovers, the standardised “Walzträger in Beton” (WIB) bridges are often used. This bridge type is frequently encountered in the Swiss railway network and impresses with its simple design, well-known load-bearing behaviour and slenderness. However, disadvantages are high material consumption (full concrete slabs with steel girders) and reduced durability (exposed lower flanges of the steel profiles). For these reasons, SBB (Swiss Federal Railways) looks for an alternative bridge system to overcome the mentioned shortcomings. A preliminary inventory analysis by SBB shows the need for such a system with minimal maintenance and route closures: It estimates that on the SBB network, around 800 existing track bridges with spans between 2 and 10m are assessed with condition classes 3 (“sufficient”) or 4 (“poor”). This means that measures will be necessary on these structures in the foreseeable future. Although not all these condition-critical bridges need to be replaced, and many new constructions will be designed as closed frames, SBB sees a great need for single-span bridges in the span range of 2 to 10m.
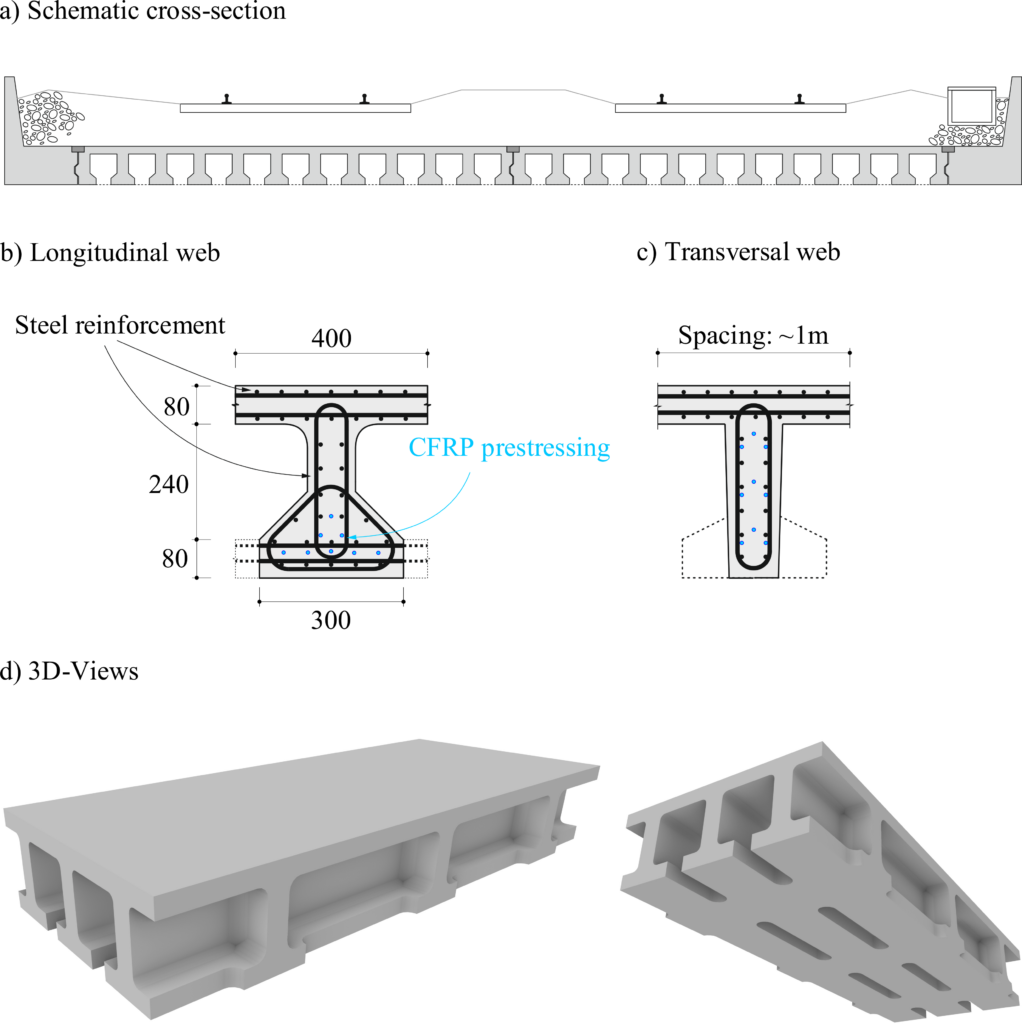
At the Chair of Concrete Structures and Bridge Design, research is conducted under the direction of Prof. Dr. Walter Kaufmann and Dr. Karel Thoma with the goal to develop a system solution that overcomes the disadvantages of WIB bridges. Design and materialisation are entirely focused on durability and fast erection (high degree of prefabrication). The basic concept is shown in Figure 1. The ultra-high performance concrete (UHPC) allows a slender construction due to its high strength, and its impermeability prevents entering of corrosion-inducing substances. Under serviceability loads, the system should remain uncracked, which reduces deformations due to the high uncracked stiffness and prevents the formation of corrosion-promoting cracks. Consequently, the bridge system is prestressed longitudinally and transversely. Pre-tensioned carbon fibre reinforced plastic (CFRP) is used for durability and monitoring reasons instead of conventional steel for the prestressing. The CFRP bars are pre-tensioned in a tensioning frame and positioned in the formwork together with the steel reinforcement. After casting and concrete hardening, the CFRP bars are released from the tensioning frame, whereby they anchor themselves in the concrete through friction and induce a normal compressive force to the concrete. Figure 2 shows schematically the pre-tensioning process, which takes place in a prefabrication factory.
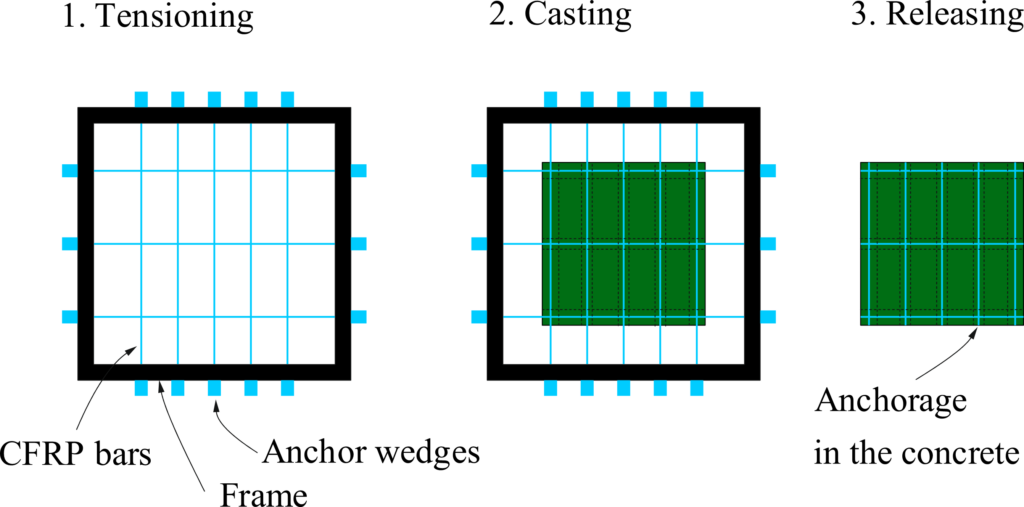
In addition to the CFRP prestressing, conventional steel reinforcement is used, as already mentioned, which provides a more ductile load-bearing behaviour. A system with only CFRP would behave approximately linearly elastic until failure. The chosen variant with a lower flange and inspection openings (Figure 1 d) allows for a slender design and an arrangement of the longitudinal prestressing bars in the flange, reducing the necessary amount of CFRP bars and separating the longitudinal prestressing from the transversal. Disadvantages – e.g. compared to an open cross-section without lower flanges – arise in the visual inspection capability during operation and in the formwork technology.
This project aims at developing a reliable system solution that will ultimately be approved by the Federal Office of Transport. To achieve this, as a first step, scientific questions related to the load-bearing behaviour of the concrete-steel-CFRP composite material, which to the knowledge of the project team has never been used for a railway bridge in Switzerland before, have to be answered. A schematic overview of the scientific questions is given in Figure 3. Particular attention is paid to the cyclic behaviour of the composite material: How does the material behave after 1, 2 or 4 million load cycles? In particular: How does the ratio of bond stresses between reinforcement and prestressing (Factor ξ according to SIA 262, 4.3.8.1.5) evolve with the load cycles? To address these questions, an extensive series of experiments together with our partners at HSLU and Empa is planned. At ETH, we focus on the tensile behaviour (see Figure 3 a) and the simulation of the bridge slab (Figure 3 e). From the tensile tests, we will extend the tension chord model (TCM) [1] to CFRP prestressing, which will allow us to model the load-deformation behaviour and the ductility of the material, including the effects of cyclic loading. The adapted TCM will serve as a basis for a universal material model, which will be implemented into a nonlinear FE framework analogously to [2] in order to perform a large-scale numerical parameter study to determine the final design of the bridge system. Prof. Dr. Giovanni Terrasi and his team at Empa work intensively on the pre-tensioning and the development of a clamping anchorage system for the CFRP prestressing. Furthermore, they will be dealing with the bond behaviour of CFRP in the anchorage region (Figure 3 c) and the cyclic behaviour of a statically determined beam in bending and shear (Figure 3 b). HSLU, under the direction of Prof. Dr. Albin Kenel, is – in addition to all questions regarding concrete technology, the systematic measurement of material properties and questions regarding curing (UHPC is very susceptible to shrinkage due to its high cement content) – concerned with the pre-tensioning frame, the redistribution of loads in the bridge in case of eccentric loading (Figure 3 d) and fire behaviour.
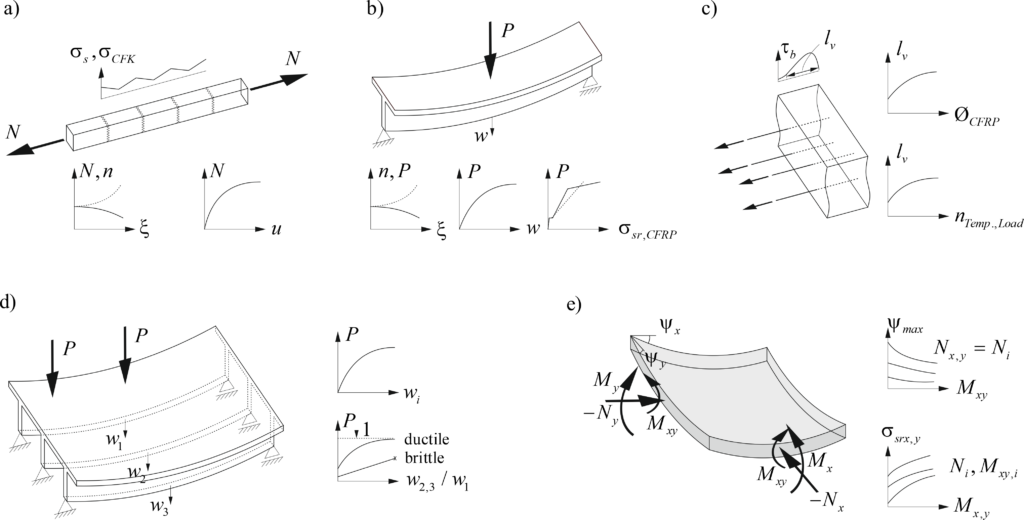
The first highlight of the project is a large-scale test on a 2 x 6m section of a bridge. The test serves as a “proof of concept” to show that (i) we can manage the construction and (ii) the mechanical behaviour permits use for the SBB. The challenge of producing this first large bridge section is taken up by alphabeton AG who is responsible for the production of all specimens in the project. The biggest challenges are the formwork and the prestressing, which requires careful planning, particularly regarding occupational safety.
The large-scale test will be carried out in spring/summer of 2022 in the construction hall at ETH Hönggerberg. We will keep you posted about the further course of the project, which will include the design of the system solution and a dimensioning tool with a subsequent pilot project on the SBB rail network, here in our blog.
References
[1] Alvarez M. Einfluss des Verbundverhaltens auf das Verformungsvermögen von Stahlbeton. Tech Rep 236, Institut für Baustatik und Konstruktion, ETH Zürich;1998. http://dx.doi.org/10.3929/ethz-a-002000033.
[2] Thoma K, Roos P, Weber M. Finite-Elemente-Analyse von Stahlbetonbauteilen im ebenen Spannungszustand. Beton- Stahlbeton 2014;109(4):275–83. http://dx.doi.org/10.1002/best.201300087.
Andreas Näsbom
Comment this post on LinkedIn or Instagram