Link zur deutschen Version: Schalungsloses Bauen von gekrümmten Betonwänden
Concrete is by far the most used building material today. Its ability to be moulded into any shape has certainly contributed to this success. From early on applications during the Roman Empire until today, fresh concrete has typically been cast into a formwork. Do you know about current research to avoid formwork when building concrete structures? In this post, I will introduce recent advances on digital fabrication processes with concrete, with a special focus on the formworkless Mesh Mould Prefabrication technology. These new digital technologies are opening the way to a more sustainable construction of optimised geometrically complex concrete structures, and could soon become standard on construction sites.
Limitations of conventional formworks for complex geometries
We have a wide range of industrial formwork systems on the market, which allow building concrete structures of simple or repetitive shapes very efficiently. The contribution of such formworks to the total environmental impact and cost of a structure is typically limited because they can be reused many times. This picture changes radically when building geometrically complex concrete structures. Such structures require very expensive, one-of-a kind formwork, which can often not be reused or even recycled.
Image credits: Fabian Scheurer, designtoproduction. Image credits: INGPHI.
The pictures above show that building geometrically complex concrete structures with non-reusable formworks is far away of being economically and ecologically sustainable. In consequence, only unique projects can afford complex geometries such as double-curved surfaces today. Many of you might think that such structures are just a niche driven by aesthetical reasons. What is therefore our interest in finding ways to build them more efficiently? We have abandoned very efficient structural systems used in the past for the sake of construction efficiency. Our ultimate motivation is making the fabrication of materially optimised concrete structures affordable and sustainable, not just enabling extravagant designs.
How digital fabrication technologies might change the way we cast concrete
The increasing digitalisation of construction brings about many possibilities to tackle the challenge of building concrete structures with increasingly complex geometry at the same cost and even with lower construction waste. This research field is known as Digital Fabrication with Concrete. It covers a wide range of topics, from robotically fabricated reinforcement and additive manufacturing of concrete to computational design tools suitable for complex geometries. Our group is very active in this field, thanks to our involvement in the Swiss National Centre of Competence in Research (NCCR) Digital Fabrication. In another post, I will introduce the wide range of digital fabrication technologies that can be used to produce concrete structures. These technologies are either formworkless or use non-standards formworks. You may have heard about concrete extrusion 3D printing, which is by far the most widely researched digital fabrication technology. In this technology, a concrete element is produced without a formwork by extruding consecutive layers of concrete on top of each other.
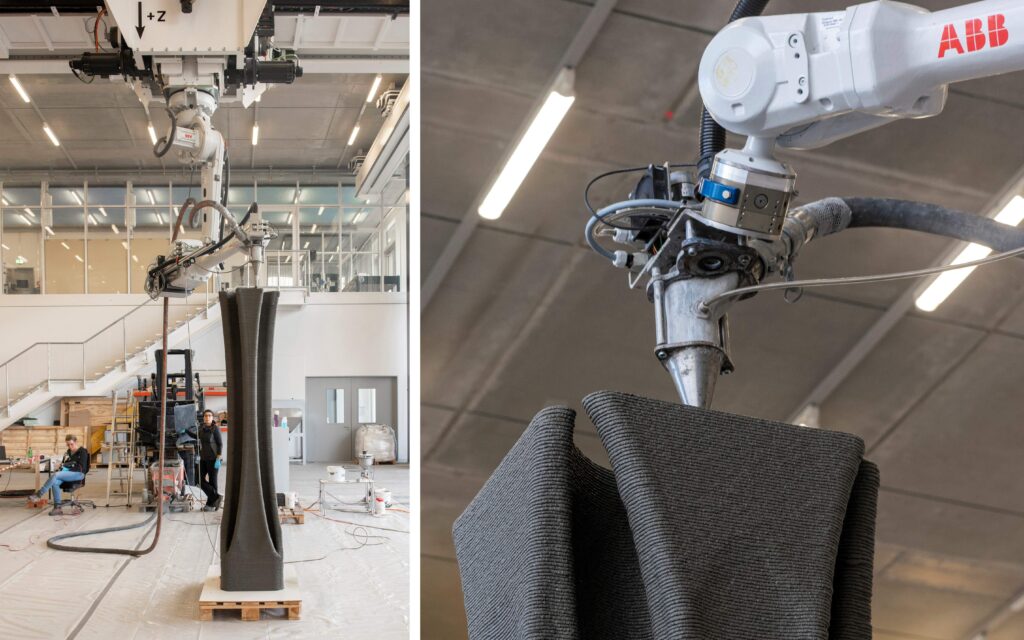
Thanks to great development in material science and technology, concrete 3D printing has reached a high degree of automation. However, building concrete structures with concrete 3D printing is still a challenge because there are no suitable strategies to integrate reinforcement, mainly perpendicularly to the printing direction. The high-tech 3D-printed walls built so far are typically unreinforced and have very low structural demands (typically single story buildings, as seen in the pictures below). They could have been built in masonry with a much lower cost and environmental impact.
Suite in Lewis Grand (Baradi 2016). R&Drone Laboratory in Dubai (Cybe 2017). Apis Cor House in Russia (Skin 2017). Apis Cor House in Russia (Skin 2017). 3D HOUSING 05 in Milan (CLS 2018). The BOD in Copenhagen (COBOD 2018).
Mesh Mould: early research
Mesh Mould is another digital fabrication process that solves the difficulties to integrate reinforcement inherent to other technologies such as 3D concrete printing and allows producing efficiently double-curved load-bearing walls. Gramazio Kohler Research at ETH Zurich came up with the Mesh Mould concept already one decade ago, by revisiting the ferrocement system patented by Pier Luigi Nervi in 1943 with innovative digital processes.
The formwork which represents the real weakness of reinforced concrete from a constructive and economic viewpoint becomes absolutely superfluous with ferrocement. The metal reinforcement made up of netting and bars can adapt with great ease to curved surfaces or any type of skewing. Its intrinsic lightness and deformability mean that it can be supported with light scaffolding, which enormously simplifies the construction of large and very large roofs
P. L. Nervi: “Scienza O Arte Del Costruire?: Caratteristiche E Possibilità Del Cemento Armato”, 1945
In Mesh Mould, a robot produces a dense reinforcement mesh. The mesh is filled with a special concrete mix that achieves sufficient compaction without flowing out the mesh.
Finally, the concrete cover is sprayed with shotcrete. While we often refer to Mesh Mould as a formworkless technology, strictly speaking, the reinforcement also serves as a stay-in-place permeable formwork. The geometric freedom of the walls produced with this technology is only constrained by the possibilities of the robotic fabrication of meshes. The great potential to build double-curved concrete structures efficiently, explains that we won the Swiss Technology Award 2016 in the category «Inventors» with Mesh Mould.
In the first phase of the project, the meshes were produced on-site by the “in-situ fabricator” robot. To test the possibilities and limitations of Mesh Mould in a real construction environment, we addressed the fabrication of a 12 m long and 120 mm thick double curved wall in the DFAB HOUSE, a residence opened in 2019 for research guests of EMPA at Dübendorf.
You can find more details of the production at the DFAB HOUSE in the video below. As you can see, the result is great but we identified several aspects to be improved during the industrial scale-up of Mesh Mould. On one hand, the casting was very labour intensive. From the structural side, the horizontal reinforcement was composed of small welded segments: a structurally inefficient solution driven by fabrication constraints.
Mesh Mould Prefabrication: industrial implementation
Thanks to the fruitful collaboration between our group, Gramazio Kohler Research and the industrial partners PERI and SIKA, we are further developing Mesh Mould to reach commercialisation. The meshes are now prefabricated in a controlled industrial environment to tackle the challenges faced in the DFAB HOUSE. Thanks to a novel, patented robotic wire application process, the reinforcement is now continuous in both directions. This automated bending and welding process enables the fabrication and layering of doubly curved meshes from steel rebar of up to 12 mm in diameter. The project includes the development of a competitive concrete mixture that ensures a robust onsite filling process providing good compaction.
We are conducting an extensive experimental campaign to determine the structural behaviour of Mesh Mould Prefabrication. Thanks to the implementation of an innovative and automated structural design approach based on the sandwich model, complex Mesh Mould structures will not only be build but also dimensioned and optimised in a very efficient manner. We hope that this and similar efforts will soon make an impact towards a leaner construction of concrete structures.
Jaime Mata-Falcón