Link to English version: Building curved concrete walls without formwork
Beton ist heutzutage bei weitem das meistgenutzte Baumaterial. Die Möglichkeit ihn in jede mögliche Form zu giessen hat sicher zu seinem Erfolg beigetragen. Von frühen Anwendungen im römischen Reich bis heute wird Beton typischerweise in eine Schalung gegossen. Kennen Sie aktuelle Forschung um Schalungen bei Bau von Betonstrukturen zu vermeiden? In diesem Post stelle ich die neusten Fortschritte in der digitalen Fabrikation mit Beton vor, mit einem speziellen Fokus auf das schalungslose Verfahren Mesh Mould Prefabrication. Neue digitale Technologie eröffnet den Weg zur nachhaltigeren Herstellung von optimierten, geometrisch komplexen Bauwerken und könnte bald standardmässig auf Baustellen verwendet werden.
Schwachpunkte konventioneller Schalung für komplexe Geometrien
Auf dem Markt gibt es eine Fülle industrieller Schalungssysteme, die es erlauben Betonstrukturen mit einfachen oder wiederholenden Formen effizient zu bauen. Der Anteil solcher Schalungen an der totalen Umwelteinwirkung und an den Kosten des Bauwerks ist üblicherweise begrenzt, da sie mehrmals wiederverwendet werden können. Bei geometrisch komplexen Bauwerken sieht das grundlegend anders aus. Solche Bauwerke benötigen oft sehr teure Unikate als Schalung, die oft nicht wiederverwendet oder sogar nicht recycelt werden können.
Bildquelle: Fabian Scheurer, designtoproduction. Bildquelle: INGPHI.
Die Bilder zeigen, dass der Bau von geometrisch komplexen Bauwerken mit Einwegschalungen alles andere als wirtschaftlich und nachhaltig ist. Daraus folgt, dass nur einzigartige Projekte sich heute komplexe Geometrien, wie zum Beispiel doppelt gekrümmte Oberflächen, leisten können. Viele von Ihnen denken wahrscheinlich, dass solche Bauwerke ein Nischenprodukt sind, das nur ästhetische Zwecke erfüllt. Warum sind wir dann daran interessiert sie effizienter zu bauen? Wir haben früher verwendete statische System mit effizientem Tragverhalten zugunsten von effizienten Bauabläufen aufgegeben. Unser oberstes Ziel ist es die Herstellung von materiell optimierten Betonbauwerken erschwinglich und nachhaltig zu machen, nicht nur extravagante Entwürfe zu ermöglichen.
Wie die Digitale Fabrikation den Betonbau verändern kann
Die zunehmende Digitalisierung im Bauwesen bietet viele Möglichkeiten um die Herausforderung von Betonbauten mit komplexer Geometrie zu gleichen Kosten und sogar mit weniger Bauabfall anzugehen. Das Forschungsgebiet heisst Digitale Fertigung mit Beton und deckt eine Vielzahl Themen ab, von robotisch hergestellter Bewehrung über die additive Fertigung von Beton bis zu rechnergestützten Entwurfstools für komplexe Geometrien. Dank unserer Beteiligung am Nationalen Forschungsschwerpunkt (NFS) Digitale Fabrikation ist unsere Gruppe in diesem Gebiet sehr aktiv. In einem zukünftigen Post werde ich das breite Spektrum an Technologien der digitalen Fabrikation, die zur Erstellung von Betonbauten genutzt werden können, vorstellen. Die Verfahren sind entweder schalungsfrei oder sie nutzen keine herkömmliche Schalung. Vielleicht haben Sie schon vom 3D-Druck mit Beton gehört, der meisterforschten Methode der digitalen Fabrikation. Dabei wird ein Betonelement schalungsfrei produziert indem Betonschichten übereinander extrudiert werden.
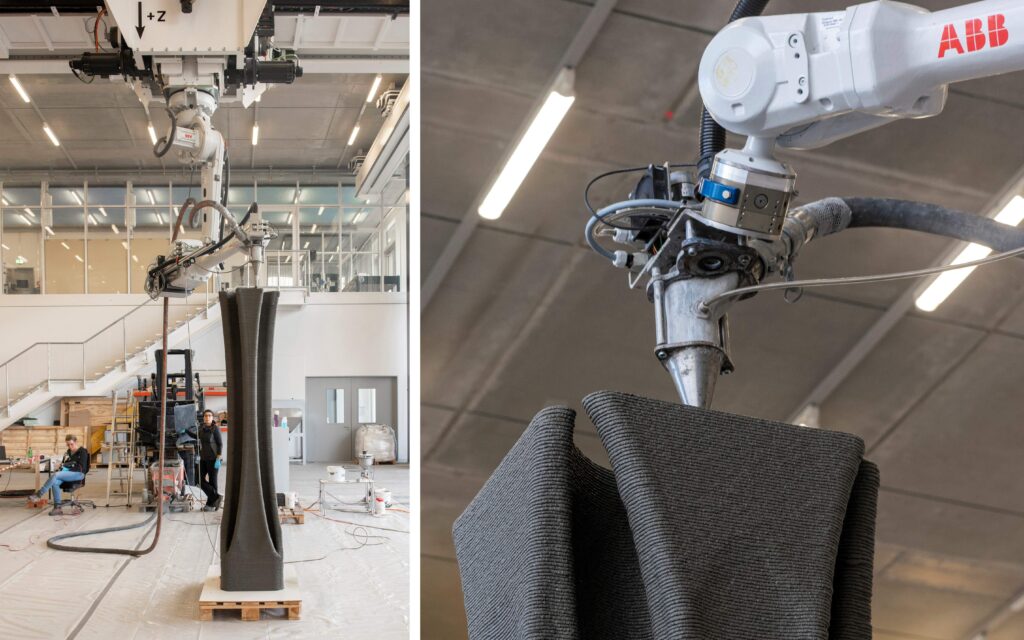
Dank grossen Entwicklungen in der Materialwissenschaft und –technologie hat der 3D-Druck mit Beton einen hohen Grad der Automatisierung erreicht. Die Herstellung von Betonbauten mit 3D-Druckverfahren ist jedoch noch eine Herausforderung, da es noch keine geeignete Strategie zur Integration der Bewehrung gibt, insbesondere in die Druckrichtung. High-tech 3D-gedruckte Wände sind bis jetzt üblicherweise unbewehrt und auf sehr geringe Einwirkungen ausgelegt (typischerweise einstöckige Gebäude, wie in den Bildern unten). Sie hätten mit viel tieferen Kosten und Umwelteinwirkungen in Mauerwerk gebaut werden können.
Suite im Lewis Grand (Baradi 2016). R&Drone Laboratory in Dubai (Cybe 2017). Apis Cor Haus in Russland (Skin 2017). Apis Cor Haus in Russland (Skin 2017). 3D HOUSING 05 in Mailand (CLS 2018). Das BOD in Kopenhagen (COBOD 2018).
Mesh Mould: Beginn der Forschungsarbeiten
Mesh Mould ist ein weiterer digitaler Fabrikationsprozess und löst die Problematik der Integration von Bewehrung, die bei anderen Technologien, wie zum Beispiel 3D-Druck mit Beton, besteht. Mesh Mould erlaubt es effizient doppelt gekrümmte tragende Wände zu erstellen. Gramazio Kohler Research an der ETH Zürich kam bereits vor einem Jahrzehnt auf das Konzept, als Weiterentwicklung des Ferrocement Systems, das Pier Luigi Nervi 1943 patentiert hat, mit innovativen digitalen Prozessen.
The formwork which represents the real weakness of reinforced concrete from a constructive and economic viewpoint becomes absolutely superfluous with ferrocement. The metal reinforcement made up of netting and bars can adapt with great ease to curved surfaces or any type of skewing. Its intrinsic lightness and deformability mean that it can be supported with light scaffolding, which enormously simplifies the construction of large and very large roofs
P. L. Nervi: “Scienza O Arte Del Costruire?: Caratteristiche E Possibilità Del Cemento Armato”, 1945
Bei Mesh Mould produziert ein Roboter ein dichtes Bewehrungsnetz. Das Netz wird mit einer speziellen Betonmischung befüllt, die eine genügende Verdichtung erreicht, ohne aus dem Netz zu fliessen.
Schliesslich wird die Bewehrungsüberdeckung mit Spritzbeton aufgetragen. Obwohl wir Mesh Mould oft als schalungslose Bauweise bezeichnen dient die Bewehrung strenggenommen als durchlässige verlorene Schalung. Die geometrische Freiheit von Wänden, die mit diesem Verfahren hergestellt werden, ist nur durch die robotische Herstellung der Netze beschränkt. Das grosse Potential zur effizienten Herstellung von doppelt gekrümmten Betonbauwerken erklärt, dass wir den Swiss Technology Award 2016 in der Kategorie «Inventors» mit Mesh Mould gewonnen haben.
In der ersten Phase des Projekts wurden die Netze auf der Baustelle vom “in-situ fabricator” Roboter hergestellt. Um die Möglichkeiten und Grenzen von Mesh Mould in einer richtigen Bauumgebung zu testen, haben wir eine 12 m lange, 120 mm dicke doppelt gekrümmte Wand im DFAB HOUSE, einer Residenz die 2019 für Forschungsgäste der EMPA in Dübendorf eröffnet wurde, erstellt.
Folgendes Video zeigen mehr Details zum Bau im DFAB. Wie Sie sehen sieht das Resultat grossartig aus, aber wir haben im grossmassstäblichen Bau einige Aspekte festgestellt die verbessert werden müssen. Zum einen war das Betonieren sehr arbeitsaufwändig. Zum anderen bestand die horizontal Bewehrung aus kleinen, angeschweissten Segmenten: eine ineffiziente Lösung aus Sicht des Tragverhaltens, die nur durch die Fertigung bedingt war.
Mesh Mould Prefabrication: Industrielle Umsetzung
Dank der ergebnisreichen Zusammenarbeit zwischen unserer Gruppe, Gramazio Kohler Research und den Industriepartnern PERI und SIKA, entwickeln wir Mesh Mould weiter um eine Kommerzialisierung zu erreichen. Die Netze werden nun in einer kontrollierten industriellen Umgebung vorgefertigt um die Schwierigkeiten im DFAB HOUSE zu umgehen. Dank eines neuartigen, patentierten, robotergestützten Drahtapplikationsverfahrens ist die Bewehrung jetzt in beide Richtungen durchgehend. Der automatisierte Biege- und Schweissprozess ermöglicht die Herstellung und Schichtung von doppelt gekrümmten Gitterstrukturen aus Bewehrungsstahl mit einem Durchmesser von bis zu 12 mm. Der Prozess beinhaltet die Entwicklung einer wettbewerbsfähigen Betonmischung, die einen robusten Füllprozess auf der Baustelle und eine gute Verdichtung sicherstellt.
Wir führen ein umfangreiches Versuchsprogramm durch, um das Tragverhalten von Mesh Mould Prefabrication zu untersuchen. Dank der Anwendung einer innovativen und automatischen Methode zur Tragwerksbemessung auf Basis des Sandwichmodells, können komplexe Mesh Mould Bauwerke effizient und im Rahmen internationaler Stahlbetonnormen bemessen und optimiert werden. Wir hoffen, mit diesem und ähnlichen Projekten einen Schritt in Richtung einer nachhaltigeren Betonbauweise machen.
Jaime Mata-Falcón