Link zur deutschen Version: Über die Verwendung von Hochleistungsfaserbeton im Brückenbau.
This post highlights the outcomes of an ongoing collaborative research project between the Universidad Politécnica de Madrid (UPM) and ACCIONA’s Construction Technology Centre, aimed at investigating the application of High-Performance Fibre Reinforced Concrete (HPFRC) in infrastructure construction. The project adopts a comprehensive approach, encompassing conceptual analysis, material development, and experimental testing. The leading UPM team is composed by Rafael Ruiz, Hugo Corres, and Leonardo Todisco. Leonardo, during this semester, is serving as a visiting professor at the ETH Zürich’s Chair of Concrete Structures and Bridge Design.
HPFRC has a compressive strength of approximately 100-120 MPa, enabling elevated prestressing levels compared to conventional concrete. This potential facilitates significant reductions in concrete volume and fosters the realisation of larger spans made in precast concrete bridges. In addition, the shear strength contributions provided by steel fibres and prestress allow to replace the conventional shear reinforcement, which represents around 40% of the mild reinforcement steel in conventional girder bridges. The research findings indicate that a fibre content of around 80 kg/m3 (Vf ≈ 1%) is sufficient to ensure adequate ductility when stirrups are removed. Additionally, the quick strength development of the cementitious matrix allows the early transmission of prestressing force, accelerating the manufacturing process. This high early-age strength is linked to a quicker development of rheological deformations, thereby reducing long-term effects, as delayed prestress losses. Finally, these mechanical performances are complemented by a notable enhancement in durability properties compared to conventional concrete.
The developed HPFRC mix, comprising 500 kg/m3 of cement, 50 kg/m3 of silica fume, and 80 kg/m3 of 4d-60 mm length steel fibres, offers promising mechanical characteristics at a cost approximately 2.5-3.0 times that of conventional concrete, significantly lower than an Ultra-High-Performance Fibre Reinforced Concrete. The developed HPFRC exhibits a compressive class C120, post-cracking bending class of 13a, and spreading class F5.
The developed HPFRC has been applied to the design of a U-shaped girder for roadway bridges (link).
The bridge superstructure comprises two U-shaped girders, each made with three 20-meters-long precast segments, resulting in a total span of 60 meters. The bridge superstructure is completed by a deck made of conventional concrete. Its cross section and 3D representation are shown in Figure 1. The prestressing is located outside the concrete, within the U girder, leading to a strong reduction of the webs and bottom slab thickness. Also, some tendons deviate at L/5 from the supports for a better approximation to the bending moment distribution.
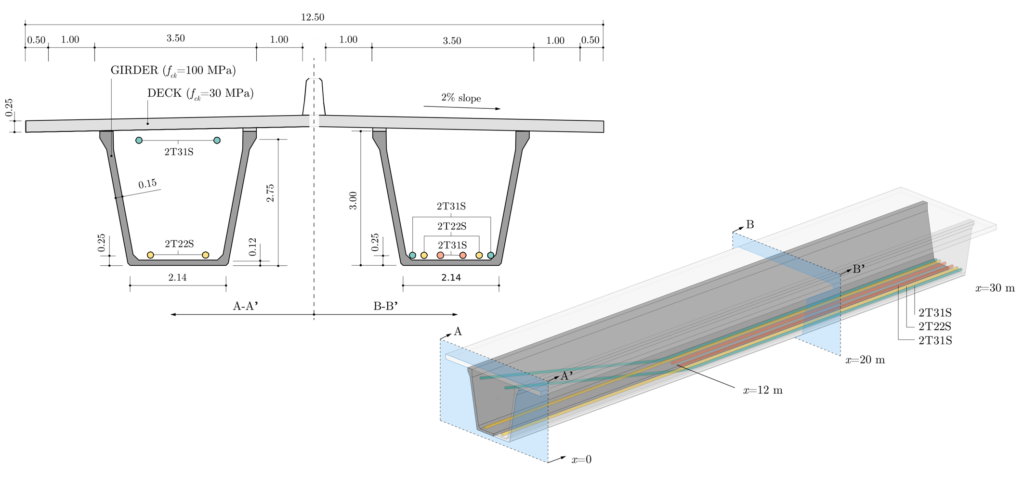
When compared with other reference projects with similar geometric features and conventional materials, the concrete consumption is reduced by 50%, the mild reinforcement is reduced by 67% and the prestressing steel increases by 17%. Overall, the HPFRC solution achieves a 14% reduction in cost, notwithstanding additional benefits such as reduced self-weight and increased durability.
To address concerns regarding cold joints between pourings and fibre orientation, two rectangular-shaped panels (Figure 2, left) were cast in 4 layers, compacted by a poker vibrator. Prismatic samples with variable orientation were extracted and the EN 14651 results (Figure 2, right) were considered satisfactory with no discernible effects attributable to fibre orientation or discontinuity planes (link).
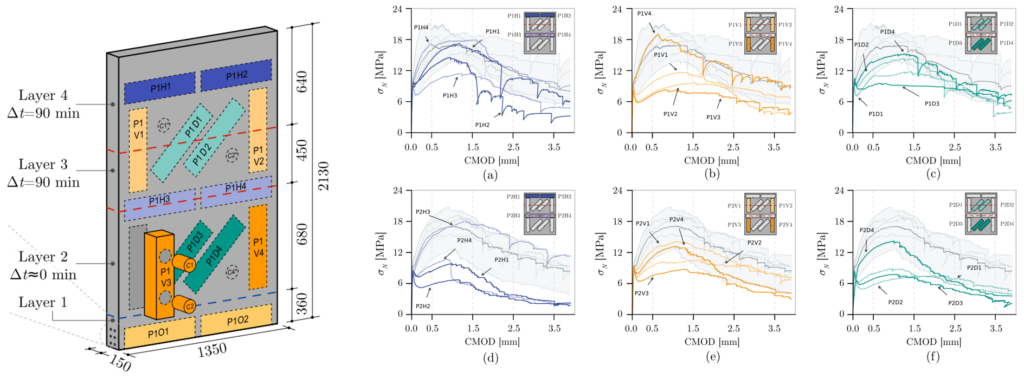
However, the shear response of such elements is still under scientific discussion and most design models provide scattered and highly conservative predictions (link), discouraging the use of HPFRC. Consequently, an experimental investigation on eight full-scale HPFRC beams was carried out (Figure 3). The beams were tested with different levels of prestressing and were instrumented with refined optical digital image correlation (DIC) measurements.
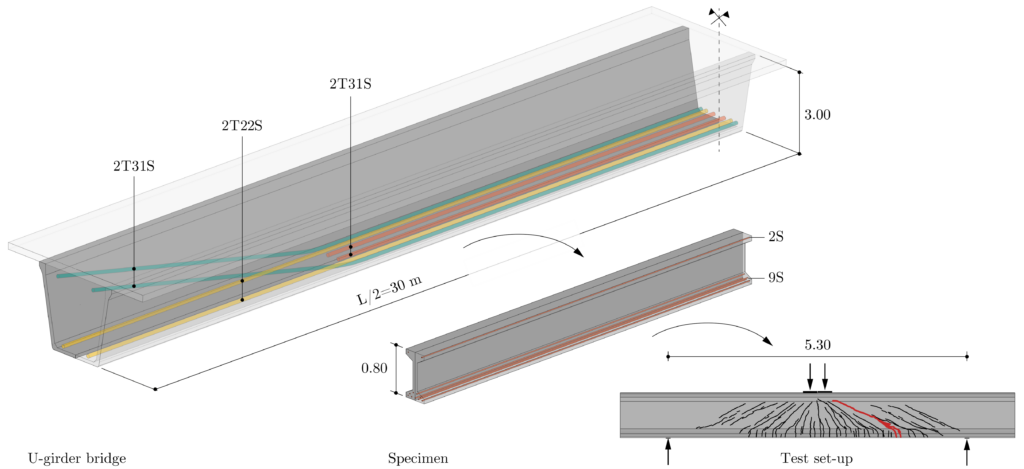
Using the experimental data, crack development and DIC-based kinematics were investigated in detail, as well as the associated contributions of potential shear-transfer actions (link). The results (Figure 4) revealed a significant contribution of the fibres, as well as of the inclination of the compression chord for high levels of prestressing, while the other potential shear contributions (i.e. aggregate interlock, dowel action) were negligible.
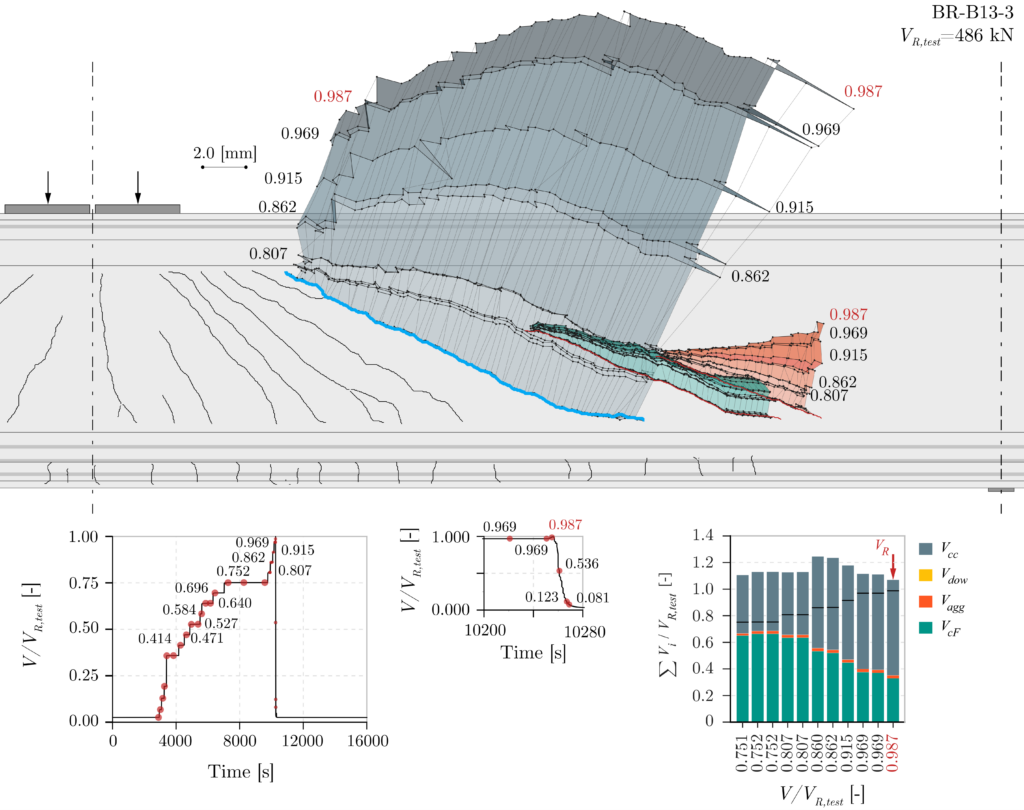
In conclusion, the study provided valuable insights into the application of HPFRC in infrastructure construction, highlighting its potential to change traditional bridge design. A 60 m-span girder bridge made of HPFRC was identified as a cost-competitive (-14% in cost) alternative to conventional solutions. It is composed of three precast segments prestressed by unbonded tendons, without the need for conventional shear reinforcement, thanks to the prestress and fibre’s contribution to shear strength. Ongoing efforts are focused on refining shear design models to better account for the unique properties of HPFRC and facilitate its widespread adoption in the industry.
Leonardo Todisco